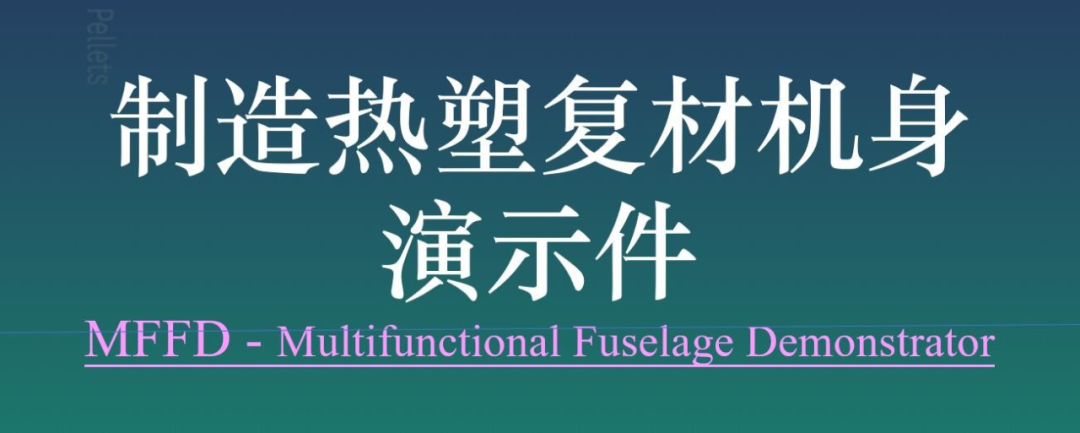
演示件的上、下壳体和组件证明了材料和新工艺可用于更轻、更便宜、更可持续的高速率制造未来飞机。
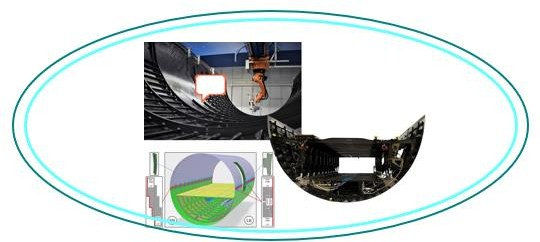
多功能机身演示器上下壳体
AFP 现场固结,焊接组装。长桁、框和角片焊接 到 MFFD 上壳体(左上)的 AFP 原位固结蒙皮上,该蒙皮将使用两个不同的纵向机身接头(左下)焊接到完整的下壳体(右)上。
多功能机身演示器( MFFD-Multifunctional Fuselage Demonstrator)计划于 2014 年构思,是欧盟资助的清洁天空 2 号(CS2-Clean Sky2)倡议(现为清洁航空)中的三个大型飞机演示器之一,旨在推进欧洲的创新技术、飞机可持续性和有竞争力的供应链。在 2017 年发布时, MFFD 计划的目标是雄心勃勃的:建造一个 8 米长、4米直径的机身段, 完全由碳纤维增强热塑性聚合物(CFRTP- carbon fiber-reinforced thermoplastic polymer )复合材料制成,能够每月生产60-100 架飞机,机身重量减少10%,经常性成本降低 20%。到 2024 年该项目结束时,这种机身的总体技术准备水平(TRL-technology readiness level)将提高到 TRL 5。
2017-2019 年,空中客车研究与技术公司(德国不来梅)作为 MFFD 项目负责人,就热塑性机身的自动化组装、焊接接头的微观力学、新型工具、多功能取放/焊接末端执行器、新的测试方法和测试、纵向机身接头、数字双胞胎等工作主题,发出了 13 份“清洁天空 2”提案 CfP07–CfP11,CFRTP 机身维修等。做出回应的财团获得了数百个工作包,由 40 多家公司和组织完成(表 1.)。吉凯恩福克公司(荷兰胡格芬)首席研发工程师萨尔瓦多·罗梅罗·埃斯特班表示:“这种多学科和国际合作是我们到 2050 年实现气候中性航空的唯一途径。”
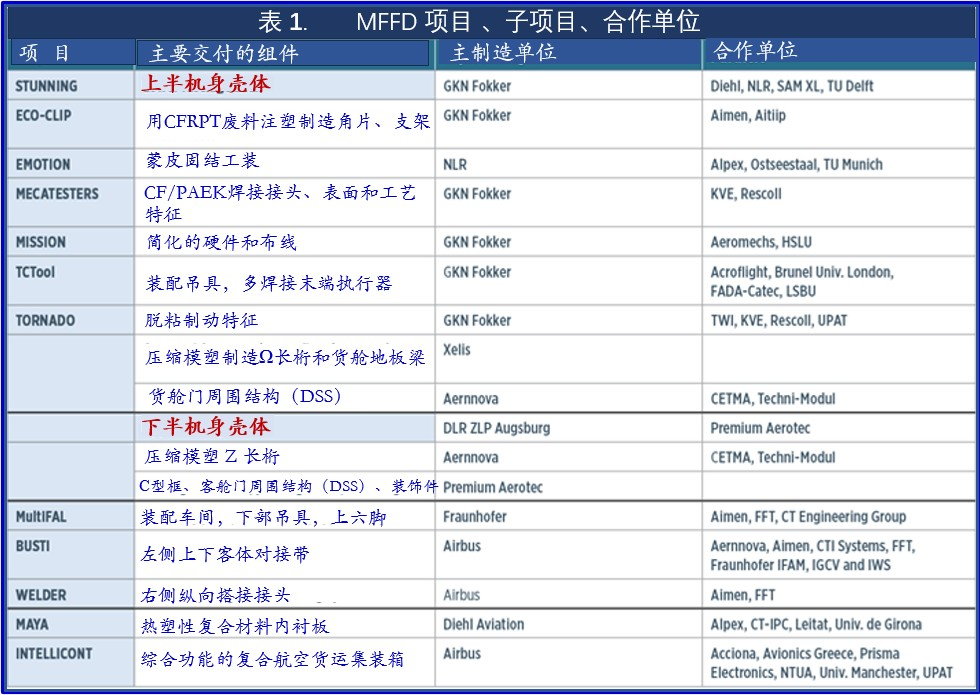
MFFD 完成的下壳体已运至 Fraunhofer 制造技术与先进材料研究所(德国斯塔德 IFAM)进行总装,上壳体应于 7 月底抵达。弗劳恩霍夫材料与梁技术研究所(德国德累斯顿 IWS)BUSTI 项目的研究员 Eric Pohl 表示:“在装配夹具中安装下壳体和上壳体需要 1-2 个月的时间。”。“我们应该能够在 8 月底/9 月初通过激光原位连接开始焊接左侧对接接头。”然 后,Aimen Centro Tecnológico(西班牙波里尼奥)和 FFT(德国富尔达)将通过超声波焊接完成右侧(右侧)搭接接头,然后对 MFFD 数字孪生进行最终评估。
本文的目的是概述迄今为止完成的 MFFD 制造步骤,并讨论将用于左侧对接带接头的激光共固结工艺。
在 STUNNING,材料测试和计算机模型被用于预测 AFP、运输和固结过程中的变形,特别是通过乘客门开口附近的许多坡道区域。
请注意,下面下壳摘要的篇幅很短,掩盖了它的复杂性——每一句话都代表了许多关于新型工具、多功能末端执行器、基于物理的模型、过程模拟、焊接经验教训等关键发展的报告。单独的下壳体自动组装方法和系统可以是自己的文章。尽管这里没有这样的细节,但请继续关注未来 CW 关于 MFFD 及其开发的技术的文章。
荷兰航空航天中心(NLR,Marknesse, Netherlands)使用 Coriolis Composites(Quéven , France)C1 机器人自动纤维铺设(AFP)系统在室温下在单个铺设工具上快速铺设(相对于 AFP 原位固结)随后的两个 90°机身段(步骤 1.)。单个象限的大小由 AFP 机器的范围决定。包括外层的雷击保护(LSP- lightning strike protection)材料,叠层设计用于在龙骨处形成斜接/锥形接头,并使用由 T700 碳纤维(CF)和 Victrex(英国兰开夏)低熔点聚芳醚酮(LMPAEK- low-melt polyaryletherketone)组成的东丽高级复合材料(荷兰奈杰弗达尔)TC1225 单向(UD)胶带。注:除非另有说明,MFFD 中的所有 CFRTP 组件均由 TC1225 UD 胶带制成。
步骤 2. 两个下半蒙皮通过龙骨处的嵌缝结合在一起,并在热压罐中共同固结
NLR 团队在位于德国斯塔德的德国航空航天中心(DLR)的研究热压罐中,在创新的高温固结模具(由 EMOTION 子项目生产)中对蒙皮和龙骨接头进行了共同固结(步骤 2)。NLR 使用热成像作为一种快速无损检测(NDI- nondestructive inspection )方法,在 2个多小时内扫描了 180°的整个下机身蒙皮。NDI 显示了航空航天质量的层压板,通过局部 C 扫描和横截面证实了这一点。然后将蒙皮运送至合作伙伴 SAM XL(荷兰代尔夫特),用于结构和内部系统的集成。
步骤 3. 连续压缩成型(CCM- Continuous compression molding)Ω长桁被传导焊接到下壳体蒙皮上,固定在下壳工装中
步骤 4. 注射成型的马鞍形角片被超声波焊接到Ω长桁和蒙皮上
步骤 5. 在热压罐中使用因瓦工具将扁平预成型件的框共同固结。腹板宽度在右侧和左侧框架的外端逐渐变细
步骤 6. 乘客地板梁采用 AFP 和热压罐固结制成
步骤 7. 对框地板组件的附加零件进行冲压,然后将其传导焊接到框和地板梁上
蒙皮被放置在 TCTool 子项目开发的支架工装中,支架工装配有 34 个支撑砧,以支持各种焊接工艺。由 Xelis(Herford,Germany)使用连续压缩成型(CCM- Continuous compression molding)制造的Ω长桁由 GKN Fokker使用 1 米长的焊接端部执行器传导焊接到蒙皮上(步骤 3)。随后,SAM XL 与 TU Delft 合作,使用 16 毫米端部执行器将角片超声波焊接到长桁和蒙皮上。
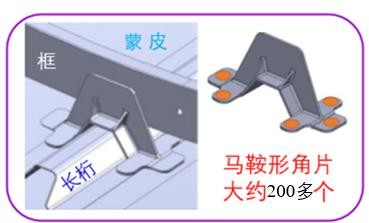
吉凯恩福克公司使用其“对接”技术制造了 12 套三个(右侧、中央和左侧)弯曲机身框,该技术将一个平腹板预成型件和两个平凸缘预成型件与面条填料在热压罐中的因瓦凹模具中共同固结(步骤 5.)。“因为我们的框没有脚,”Romero Esteban 解释道,“我们将腹板预成型件延伸到凸缘之外,为面条填料创造空间,也为在壳体组装过程中焊接地板梁创造空间。”在固结后(未来将在热压中进行),弯曲的腹板被修剪。
GKN Fokker 还使用 Mikrosam(马其顿普里勒普)机器人 AFP 系统制造了客舱地板梁,并将其牵引到成型钢芯轴上(步骤 6.)。如“MFFD 热塑性地板梁”中所述,每个叠层被分开以生产两个地板梁预制件,然后在热压罐中固结。然后将完成的地板梁焊接成组件,如下所述。
为了为货物和乘客地板提供支撑,吉凯恩福克公司使用冲压成型制造了 100 多个支柱、型材和其他连接结构,有七种不同的几何形状。然后,它将它们相互传导焊接,并将弯曲的机身框传导焊接,以创建框子组件,并将其传导焊接到地板梁,以创建地板梁子组件(步骤 7)。在 SAM XL,然后将框架子组件超声波焊接到环保夹上(步骤 8.)。
图 2 . 传导焊接下壳体组件。框架子组件(黄色)和地板梁子组件(紫色)由吉凯恩福克公司在荷兰胡格芬的吉凯恩航空航天全球技术中心(蓝色)使用其机 器人传导焊接系统进行焊接。SAM XL 自动超声波焊接框架组件至下壳体(蓝色)。GKN Fokker 使用 GKN 新的焊接头将地板梁组件导焊接到壳体上,焊接头带 有加热杆元件和用于反压力的砧座(橙色)
步骤 8. 将框架组件超声波焊接到马鞍形角片上
步骤 9. 成品 MFFD 下机身,带有导电焊接的地板梁组件和集成座椅滑轨、电气和空调系统组件
步骤 10. AFP 原位加固上半壳蒙皮
同时,12 个地板梁组件与地板格栅下部结构连接在一起,包括两个铝制座椅轨道、MISSION 项目中开发的电气系统和空气系统导管,这是 MFFD 演示预装机身外壳模块焊接组装任务的一部分。最后一步是使用 GKN Fokker 获得专利的新型传导焊接工艺将地板格栅结构焊接到框和下壳体上,该工艺包括一个带反压砧的加热棒元件(图 2)-完成 800 多个接头和 500米的焊接(步骤 9.)。
MFFD 上壳体的蒙皮由 DLR 结构研究所和轻型生产技术设计中心(ZLP,Augsburg)生产,使用 AFP 原位固结。在这个过程中,TC1225 UD 胶带在一个步骤中即可完全固结,无需进一步的真空装袋、烤箱或热压罐(第 10 步.)。弗雷德里克·菲舍尔说:“与使用热固性环氧树脂的典型 A350 机身蒙皮相比,这可将蒙皮交付时间缩短 40%。”。“然而,这个过程要求更高,因为你没有第二个整合步骤。”
“例如,”德国航空航天中心负责上壳 AFP 蒙皮生产的研究工程师 Dominik Deden 解释道,“在应用的胶带中不能有间隙和重叠,因为这些间隙和重叠会成为结构中的空隙。它们还会导致每个层的表面粗糙,并对热控制产生负面影响。因此,路径规划必须适应各自的 AFP 参数,以确保足够的层压板质量。”
ZLP 开发了一种在线检测系统,专门用于现场工艺。德国航空航天中心的 AFP 和原位过程控制进展专家 Lars Brandt 说:“我们在 AFP 末端执行器上有一个传感器系统,可以记录生产过程中的间隙和重叠。”他指出,工艺参数之间存在巨大的相互依赖性:“它们直接影响胶带的厚度和宽度,进而影响胶带如何正确地并排放置,进而影响激光功率闭环控制的热成像。因此,我们必须确保机器人末端执行器始终处于最佳温度、压力和速度。”
DLR 进行了广泛的模拟和参数试验,以建立最佳零件质量和高沉积率所需的工艺窗口。它用 70 多层胶带原位固结了一个全尺寸的测试壳蒙皮,并分析了收集的传感器和工艺数据。Brandt 说:“由此,我们开发了最佳时间-温度曲线,并与层压板的机械性能进行了比较,如层间剪切强度(ILSS- interlaminar shear strength)。”“由于工艺参数的复杂相互作用,这项工作仍在继续,但我们的目标是在年底前对现场质量进行最终评估。”
对于最终的 MFFD 上壳体,德国航空航天中心于2023 年 2 月使用 AFPT(德国 Dörth)的多牵引 AFP头、用于加热的 Laserline(德国 Mülheim-Kärlich) LDM 二极管激光器和 Grunewald GmbH&Co.KG(德国 Bocholt)提供的叠层工具完成了现场固结蒙皮。AFP末端执行器可以放置三根 0.5 英寸宽的丝束,可能的吞吐量高达 4.4 公斤/小时,最短生产时间为 32 小时。Deden 说:“材料带的数量可以很容易地增加,以实现更快的铺放和每月 70 至 100 架飞机的生产率。”上壳蒙皮还包括 LSP- lightning strike protection 膜作为第一层。
步骤 11. 使用连续超声波焊接将压缩模塑 Z 形长桁连接到蒙皮
上壳体的 Z 型长桁由 Aernnova(西班牙米尼亚 诺)提供,该公司与意大利布林迪西的 CETMA 公司合作,采用 CCM 工艺制造(见“CETMA 研发”和 “Leonardo 和 CETMA”)。DLR 使用超声波点焊来集成能量导向器——沿着每个长桁底部的一层额外的未增强 LMPAEK 树脂——这有助于控制焊接界面的能 量。同样的机器人末端执行器,经过微小的修改,也用于将 46 个 Z 形长桁集成到蒙皮上的连续过程(步骤 11.)。
Fischer 说:“这是世界上第一次通过全自动连续超声波焊接在现场固结蒙皮上进行长桁焊接,使用基于相机的路径校正,速度为 1.4 米/分钟。”。“我们能够在试片测试中证明 38 兆帕的可重复焊接强度。”
步骤 12. 电阻焊桥将压模 C 型框连接到蒙皮上,然后在机器人上(右上)电阻焊角片作为长桁和框之间的剪切连接
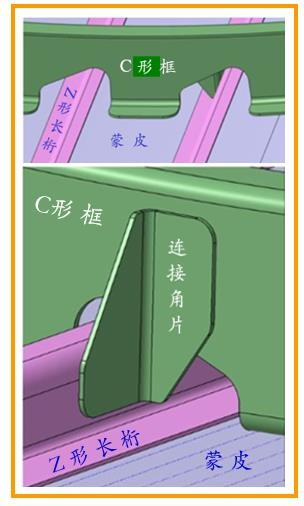
接下来,使用 DLR 开发的焊接桥将由 Premium Aerotec(PAG,Augsburg 和 Bremen,Germany)生产的 24 个一次性模压 C 型框架电阻焊接到上壳体蒙皮上(步骤 12)。电机驱动桥安装在叠层工具的上侧,能够自动运输框架并将其定位到外壳上的精确集成位置。该桥包含 14 个焊接模块,这些模块沿 C 形框架向每只脚依次施加高达 1.2 兆帕的压力。
DLR 电阻焊接专家 Manuel Endrass 表示:“然 后,模块将电流施加到位于每个框脚和蒙皮之间的焊接元件中。”焊接元件由 Toray CETEX TC1225 预浸料与 T300JB 碳纤维在 5 丝缎织物中制成,该织物与 UD 带皮中的 LMPAEK 基质相同,以及 CETEX TC1225 EC5 E-玻璃 4 丝缎预浸料制成。后者用于防止焊接部件和焊接元件的纤维取向对齐的短路。电流流过焊接元件并产生热量,使焊接界面中的基体熔化。一旦电流被切断,焊接就会冷却,同时保持压力。Fischer说:“我们展示了在 5 分钟内焊接整个框架的可扩展性。”。“这种坚固的技术提供了全表面连接,焊接强度与冲压固结参考的焊接强度相等。从本质上讲,我们的电阻焊接可以理解为一种小型化的冲压工艺。”
在框之后,德国航空航天中心再次使用电阻焊接将角片整合为 Z 形桁条和弯曲机身框架之间的抗剪连接件(步骤 12.)。Endrass 解释道:“德国航空航天中心开发了一种基于机器人的 cobot 焊接系统,以适应高度受限的空间。”。“这项开发背后的想法是在不知道确切竣工条件的情况下自动集成防滑钉。因此, LBR iiwa cobot[德国奥格斯堡 KUKA 机器人公司]凭借其顺应性控制的转向能力,将在没有任何初步零件测量或机器人示教的情况下自动对准。由于焊接力是通过末端执行器的闭合力通量设计施加的,因此可以在不引入外部载荷的情况下集成角片。”德国航空航天中心计划在 7 月底前将上壳交付给弗劳恩霍夫 IFAM。然而,它在电阻焊接和原位固结方面的工作仍将继续。
步骤 13. 先进的激光原位连接将用于将六个对接 带层压板共同固结到机身外壳上,形成左侧机身纵向接头
步骤 14. 右侧搭结机身接头将通过连续超声波焊接形成。电阻焊接框连接板(顶角)将连接上下框架和蒙皮
上下外壳对合装配夹具。该夹具是在 MultiFAL项目中开发的,用于组装 MFFD 机身外壳,包括一个用于下外壳的支架和调整六足系统(黄色,机身顶部),用于调整外壳以进行连接
MFFD 下壳和上壳的组装将从左侧对接带纵向机身接头开始,该接头已在 BUSTI 项目中开发(步骤 13)。在空中客车公司的领导下,它包括合作伙伴 Aernnova、Aimen、CTI Systems(卢森堡 Lentzweiler)、 FFT 和 Fraunhofer IFAM、IGCV 和 IWS。右侧搭接机身接头将由 FFT 和 Aimen 通过 WELDER 项目使用超声波焊接完成(步骤 14.)。组装夹具是在 MultiFAL 项目中开发的,它将在连接过程中将下壳体和上壳体固定在一起,包括下壳体的支架和用于定位和调整上壳体位置的 10 个调整六足系统。带有六轴力和扭矩传感器的真空夹具将在光学测量系统的引导下调整外壳的姿态和形状,以管理组装过程中的公差。
首先放置下壳,然后放置上壳。六足系统将根据连接过程将外壳调整为正确的几何图形。在机身内部,弯曲以匹配机身的大型铝块(“内部定位器”)将沿径向向外挤压,以抵抗焊接末端执行器在连接过程中施加的固结压力。
Pohl 解释道,对于 BUSTI 项目和右侧对接带接头,Fraunhofer IWS 开发了一种称为激光原位连接(CONTIjoin 用于连续连接)的工艺,“但实际上这是 CFRTP 对接带层压板与匹配机身壳体的连续共固结。”,除了确保表面没有加工灰尘等,不需要对连接区域进行预处理。“这与 AFP 固结过程非常相似,”他说。“不需要进一步的后处理,但我们使用的不是单层胶带,而是 6 层完全固结的层压板。”
图 3. 激光原位连接(CONTIjoin)工艺。Fraunhofer IWS 实验室设置展示了如何将 6 层对接带层压板引入并应用于接头区域,通过振荡激光束加热,并在固结辊的压力下,在冷却时与基底共同固结
波尔继续说道:“我们还使用了二氧化碳激光器,而不是 AFP 典型的光纤激光器。”“这是因为 LMPAEK 聚合物在这些激光器通常使用的 1060 纳米波长下几乎没有能量吸收。因为我们需要足够的吸收来熔化表面基质进行连接,所以我们使用 10.6 微米波长的 CO2 激光器,以确保聚合物基质在表面更好地加热,同时减少通过层压板的迁移。“因为对接带层压板从第一个 60 毫米到最后一个 360 毫米逐渐变宽,所以 CO2 激光器与高速扫描系统相结合,该系统可以在焊缝宽度上振荡能量束。Pohl 说,激光束本身无法跨越背带的宽度,但激光束的能量强度也在其中心,并在激光焦斑之外降低。这是一种高度动态的光束振荡,可以在接头的整个宽度上加热,最高可达 360 毫米。
CONTIjoin 工艺设备使用两种光学装置。一个是振荡激光器,另一个包括高温计和第二个扫描仪,用于测量连接处的温度(图 3)。波尔解释道:“高温计的目标是夹点,用于调整激光功率,以保持所需的工艺温度(350-370°C )。”。然而,这个咬合点实际上是一条横跨臀带宽度的线。他补充道:“因此,我们将高温计与高速扫描仪结合起来,这样我们就可以根据高温计的测量位置调整目标。”
“振荡激光束加热接合区域的表面,”波尔继续说道,“扫描高温计装置根据对接带层压板的宽度测量我们设置的不同点的温度。我们发现,在层压板中间使用一个 60 毫米宽的点就足以均匀控制过程。对于较宽的层压板,我们需要为每增加 60 毫米增加一个测量点。因此,对于第二步层压板,即 120 毫米宽,我们使用两个高温计点,240 毫米宽的带子使用四个点,等等。”高温计根据其数字控制系统跳过这些测量点,在那里可以单独设置距离和时间。Pohl 指出,“在这种情况下,各个流程之间的同步对于最终的合并质量至关重要。”
来自每次测量的温度信息提供给一个单独的控制电路,以调整该点的激光功率。波尔说:“假设我们的设定温度为 350°C ,高温计的测量温度为 340°C 。”“然后将其输入比例-积分-微分(PID- proportional integral derivative)控制回路。PID 控制器识别出其低于设定温度,并增加激光功率。增加的量已在早些时候通过工艺参数试验确定,并编程到 PID 中。”
如上所述,对接带包括六个逐渐变宽的带,一次施加一个。这与上下外壳中的一组台阶相匹配。空客公司称之为阶梯式连接结构,也用于复合材料飞机结构的粘接和焊接维修。因此,焊接对接带的区域正好适合容纳对接带的阶梯区域。波尔说:“这是连接这些外壳的一个很好的设计,因为你将共同固结或焊接到材料的厚度中,这样你就可以在接头的所有层中获得更多的表面积。”
Pohl 的团队将在客舱(乘客)门开口的每一侧连续应用六个更宽、6 层、1.2 毫米厚的固结多向对接带层压板,总共 12 道焊接道次。前四个对接带层压板由 Aernnova 使用 AFP 和真空袋固结制成。它们的特点是有一个下降区域,在那里它们的厚度减小,并在机身蒙皮的斜坡上结束。最后两个也是最宽的对接带层压板由 Fraunhofer 铸造、复合材料和加工技术研究所(IGCV,Augsburg,Germany)使用 AFP 制造,并在双带压机中固结。门两侧的这些带子都是斜切的——它们在朝向客舱门开口的最宽矩形部分和远离门的狭长部分之间有 45°的过渡。Pohl 解释说,这只适用于最后两个对接带层压板,因为它们是最长的,从舱门开口(这削弱了机身结构,需要更大的接头才能提供更大的刚度)一直延伸到 8 米长的演示机的末端,在那里不需要额外的宽度。左侧单条带子的最大焊接长度为 4.5 米,由乘客门开口中断,其中右侧搭接接头将横跨 8 米机身的整个长度。
对于每个对接带层压板,将额外铺设一层 LM PAEK 薄膜。Pohl 说:“这提供了更多的基体材料,可以实现更好的焊接和焊接强度。”。“它还产生了更可复制的焊接工艺和质量,因为我们有一个可控的基体表面厚度。”高焊接强度的另一个必要条件是在连接中固结材料的压力。这是通过固结工具来应用 的,该固结工具基本上是分段式滚筒。波尔说:“我们能施加的最大力是 10 千牛顿,这是客舱门开口周围的极限,因为这些铝制内部定位器的设计目的是在不超过允许偏转的情况下处理这种力。但例如,对于 60毫米宽的带子,我们只使用了 2.8 千牛顿。”
施加的力的大小是如何确定和控制的?波尔说:“我们已经通过参数筛选开发出了这一点。”“我们需要更大的力来制作更宽的带子,因为我们有更多的面积。看起来宽度翻倍需要两倍的力,但这种关系并不是完全线性的。所以,我们不需要 360 毫米宽带子和60 毫米带子的六倍力,我们可以用更少的力。但现在,我们正在评估这个最佳点在哪里,因为你可以按压得太用力,从而在加热过程中破坏层压板。”
CONTIjoin 用于固结工具的分段式压机
固结辊设计用于在层压板厚度变化和机身弯曲几何形状的整个过程中施加一致的压力。Pohl 解释道:“每个滚轮节段的高度通过分段滚轮中心核心内的中心框架中的凸轮轴进行调整。”。“每个滚子段都有一个柔软的弹性体套筒,可以增加接触面积。”
Fraunhofer IWS 为评估使用 CONTIjoin 工艺的共固结接缝的强度而进行的开槽搭接剪切试验结果表明,可以实现 30 兆帕的可靠平均强度。几乎所有样品都表现出一定程度的基底失效,表明接头强度高,并且主要在对接带层压板的+45°和-45°层之间失效。在随后的层间剪切强度(ILSS- interlaminar shear strength)测试中,接头显示的值为压力固结参考值的 93%。
波尔说:“我们花了很多时间进行试验,以评估最佳工艺参数,同时,我们已经建立了焊接装置。” BUSTI 团队计划于 7 月在斯塔德的 IFAM 完成焊接装置的安装,并于 8 月调试 CONTIjoin 设备和工艺,为计划于 9 月开始的左侧接头焊接做准备。
随着 MFFD 的发展,Fraunhofer IWS 已经在进一步推进 CONTIjoin。2022 年底,该公司与空中客车公司开始了另一个项目,该项目由德国政府资助,旨在开发复杂曲面的激光原位连接工艺,而不是 MFFD 机身的单一曲率。波尔说:“我们现在正在研究固结工具的概念,但我们也必须开发转向和软件。只要有一个曲率,我们就可以在加工之前设置路径。但现在,我们必须开发一种测量精确复杂曲率的方法和软件,以计算激光束在给定时间间隔内如何在接缝宽度上移动。”。“该项目将于 2026 年完成。
CONTIjoin 只是 MFFD 启用的一种技术。空中客车公司的 York C.Roth 博士是清洁航空/清洁天空 2 号大型客机平台的领导者,他说:“欧洲已经有 40 多项技术成熟。”。“MFFD 是一个杰出的例子,说明了如果学术界、研究中心、行业原始设备制造商和供应商联合起来,在一个共同的目标上保持一致,可以取得什么成就。仅靠一个合作伙伴永远无法交付如此复杂的大型演示器。”
这个演示者正在建立一个新的知识库,从中可以为未来的飞机做出决策。“MFFD 项目中展示的技术砖有助于更好地理解作为机身主要结构材料的热塑性复合材料,”位于不来梅的空中客车公司机身研发人员、MFFD 项目负责人 Ralf Herrmann 说。“通过新型连接技术和自动化技术,我们开发了一系列设计解决方案、制造和组装概念。这些将使 MFFD 的工业合作伙伴能够选择最合适的技术,以实现未来航空所需的性能改进和生态足迹减少。”
注:原文见,《Manufacturing the MFFD thermoplastic composite fuselage》2023.6.26
杨超凡 2023.6.30
原文始发于微信公众号(复合材料体验馆):制造热塑复材机身演示件