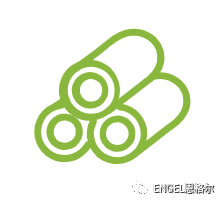
芯层和带材如何合并形成座椅底座
新型座垫底座的两层外层由热塑性UD玻纤带材制成。在两层之间注入聚丙烯(简称PP),以便模具开启后,轻量化部件成品能够顺利从模具中取出。带材和注塑材料由相同的基底材料组成。通过准确的工艺控制,可确保在注射过程中,覆盖层与注塑材料之间形成紧密的结合。
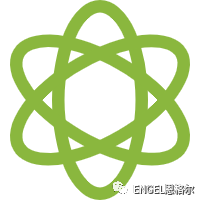
使用基质材料的简化解释😀
带材和注入芯由相同的材料制成。这意味着,当加热的PP注射进型腔时,热量同样也会融化部分带材。当它冷却时,就会产生一种连接,在这种连接中,芯层和带材之间没有明显的区别。
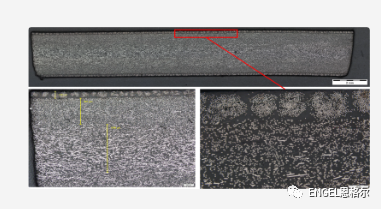

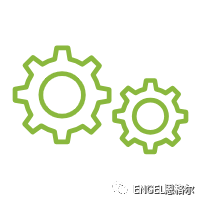
相同强度下 零件薄度升级
这种夹层结构使得开发非常薄的组件成为可能,同时又不会失去我们熟知的单片组件的抗弯强度(单片=由一种材料组成)。我们以此方法与KTM技术公司共同完成了新一代摩托车座椅。从正确选用材料、合适的组件设计到严格把控工艺管理,我们成功地将座椅的厚度减少了近30%,同时保持了至少相同的刚性。由于采用了新的材料结构,座椅的安装空间节省了65%。因此,新研发的座椅明显更为轻薄,重量减轻了30%左右。
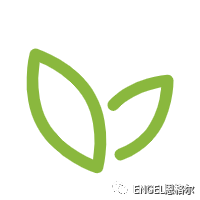
可持续发展的积极底线
减少材料的使用意味着GWP(全球变暖可能性)减少了30%。如果用生物基PP代替化石基PP用于注塑成型,全球变暖的可能性甚至可以降低85%。由于整个工作台是从相同的基体材料生产的,组件可以在其生存周期结束时进行材料回收。所有配备适当模具的ENGEL注塑机都适用于生产带夹层组件。图中所示的摩托车座椅是由客户在victory 500注塑机上生产的。
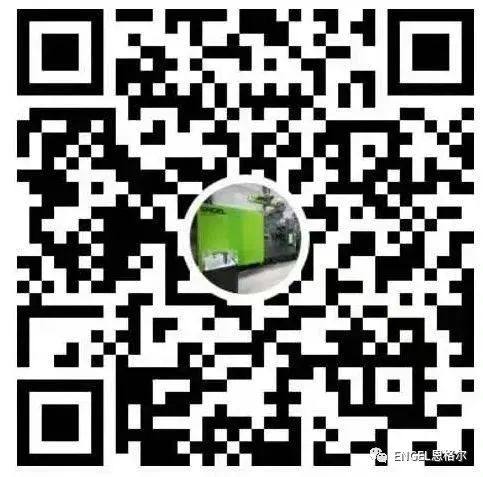
ENGEL
原文始发于微信公众号(ENGEL恩格尔):KTM技术与ENGEL紧密合作,实现高瞻远瞩的解决方案