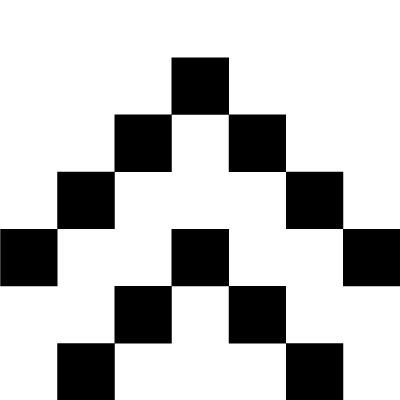
点击“蓝字关注我们

◆ ◆ ◆ ◆
连续纤维增强复合材料轻量化动力电池箱上壳体的
常见工艺路径
◆ ◆ ◆ ◆

现阶段,“以塑代钢”的轻量化思路受到汽车行业的广泛关注,并成功在多个车型、多种部件的量产方案中得到应用。其中,纤维增强复合材料方案具有比强度高、质量轻等优点,成为汽车轻量化的一个重要技术方向。随着复合材料成型工艺类型不断丰富以及高效率自动化生产装备的不断推出,可满足汽车量产节拍的连续纤维复合材料成型工艺制造方式,已趋于成熟。
对于纯电动汽车来说,减重是提升其动力和续航的一个有效途径。作为其中的一个大体积部件,电池箱存在着相当大的轻量化潜力。以电池箱上盖为例,市面上已存在多种“以塑代钢”的轻量化方案,包括SMC、LFT-D和纤维增强注塑等工艺的应用。然而,这些方案主要以非连续纤维增强的复合材料为主。由于产品性能要求和工艺本身的限制,上述方案的制品壁厚通常在2.5mm以上,进一步实现薄壁化存在较大的技术难度。由于上述工艺在薄壁化方面的局限性,越来越多的汽车主机厂和汽车电池厂商将关注点放在了连续纤维增强复合材料的电池箱方案上。在轻量化设计方案中,最常被选用的工艺路线是连续玻纤和阻燃快速固化树脂/阻燃工程塑料组合的轻量化方案。这种轻量化技术能够满足了电池箱上盖本身对于阻燃、密封、绝缘、隔热以及力学性能的要求,同时连续纤维材料能够提供更加优良的力学性能,使得产品厚度得到了有效地降低,从而达到了更好的减重效果。
1.注塑模压一体成型(Fiberform)工艺
热塑性塑料的种类繁多,特性多样,且改性空间较大。因此,将连续纤维引入热塑性材料中,一直是热塑性复合材料的重要研究方向。Fiberform工艺提供了其中的一种方式,并且已经在不少量产成型中得到了应用。Fiberform工艺通过生产装备的改进和配合,将热塑性有机板材模压和注塑工艺相结合,在受力大的位置引入连续纤维对产品进行增强,同时保留了注塑工艺能够成型复杂结构的特点,是一种高效率制造轻量化结构制件的工艺路径。
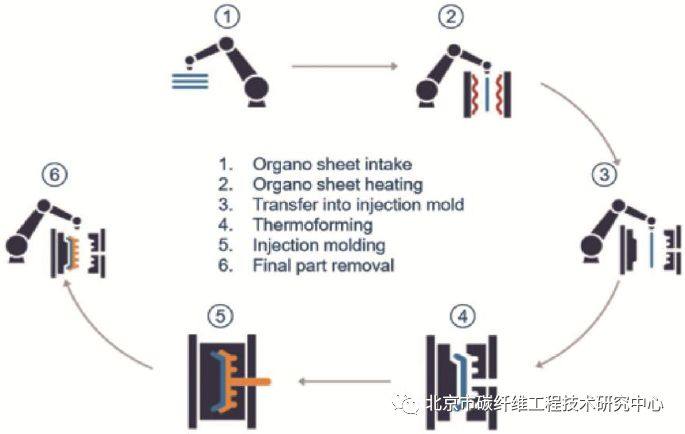
图1. Fiberform工艺流程
(图片来源: 北京市碳纤维工程技术研究中心、KraussMaffei)
Fiberform工艺首先使用机械手将有机板材(热塑预浸片材层合板)抓取置于红外加热炉中,加热变软后放入模具中并使用模具中的机构对其进行定位,然后闭合模具进行热料冷模的模压过程,在合模后通过注塑充满剩余模腔,冷却脱模后完成产品的成型。
电池箱上盖为盒状结构,几乎没有局部激变的特征,可进行大面积的连续纤维板材增强。在有机板材拼接以及无板材增强的位置,塑料通过注塑过程注入进行熔接填充。加强筋结构应用在整个产品中,其密度和尺寸根据增强板材的位置而确定。Fiberform工艺在产品中引入了连续纤维,在保证性能的前提下,达到了可观的减重效果。现阶段,北京市碳纤维工程技术研究中心(下称“中心”)正以KraussMaffei GX650-4300注塑模压一体设备为基础,打造使用Fiberform工艺开发制造电池箱产品的全流程技术路线。中心将通过电池箱项目的开发经验,以点带面,集中国内外优质资源,开发更多汽车轻量化部件的解决方案。
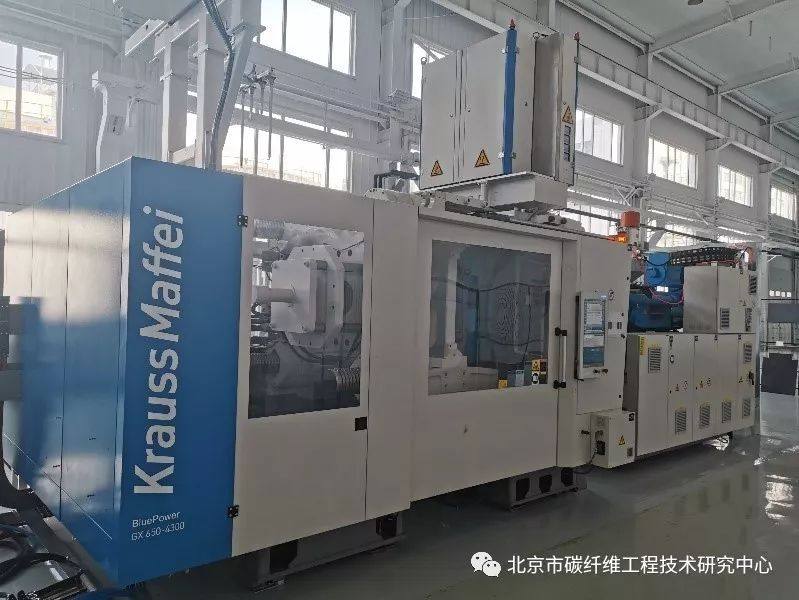
图2. KraussMaffei GX650-4300设备
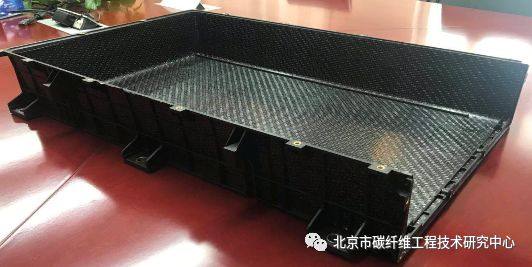
图3. 某款Fiberform工艺标准箱电池包产品
2.高压树脂传递模塑(HP-RTM)工艺
通过成套生产装备的配合、材料性能和固化工艺的改进、模具结构的设计以及工艺参数的调整,采用高压树脂传递模塑工艺使得RTM工艺节拍从常规的数小时/件缩短到达到几分钟。从表面上来看,HP-RTM区别于传统RTM的是高压,但从本质上来看,则是生产节拍的大幅度提升。
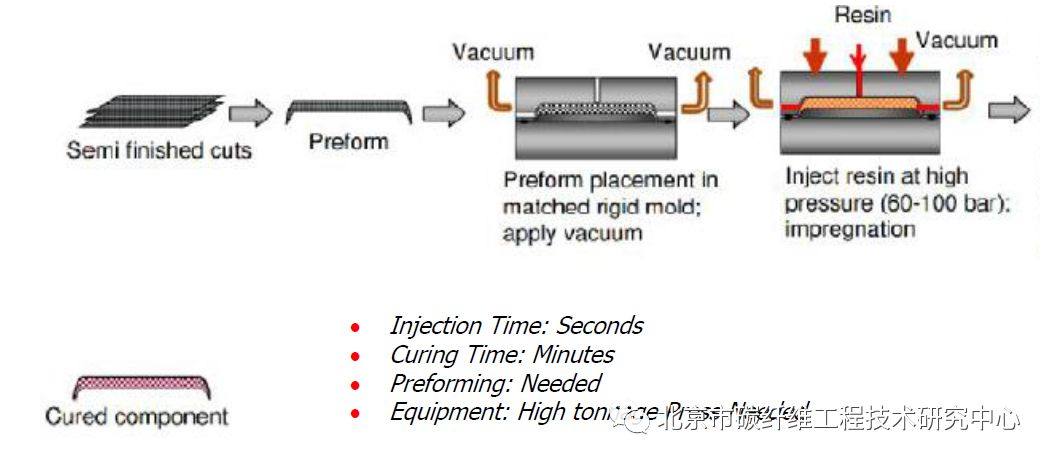
图4.HP-RTM工艺流程
(图片来源:CANNON)
HP-RTM工艺首先使用多层裁切的方式进行下料,然后通过加热后冷压的方式,对有定型剂的织物堆叠进行预成型,得到具有产品形状的织物预制体。预制体置于模具中,模具闭合后以较高压力注入树脂。待树脂完全固化后,产品取出即完成一个节拍的制造。在理想状态下,HP-RTM的节拍可达到3~5min。
对于电池箱上盖产品来说,其中一种HP-RTM方案是采用连续高模玻纤织物和快速固化阻燃聚氨酯(PU)树脂进行制造。聚氨酯树脂经过改性,在保留本身韧性好的优点同时,具备了阻燃和快速固化的特性,且可以满足HP-RTM的工艺性要求。
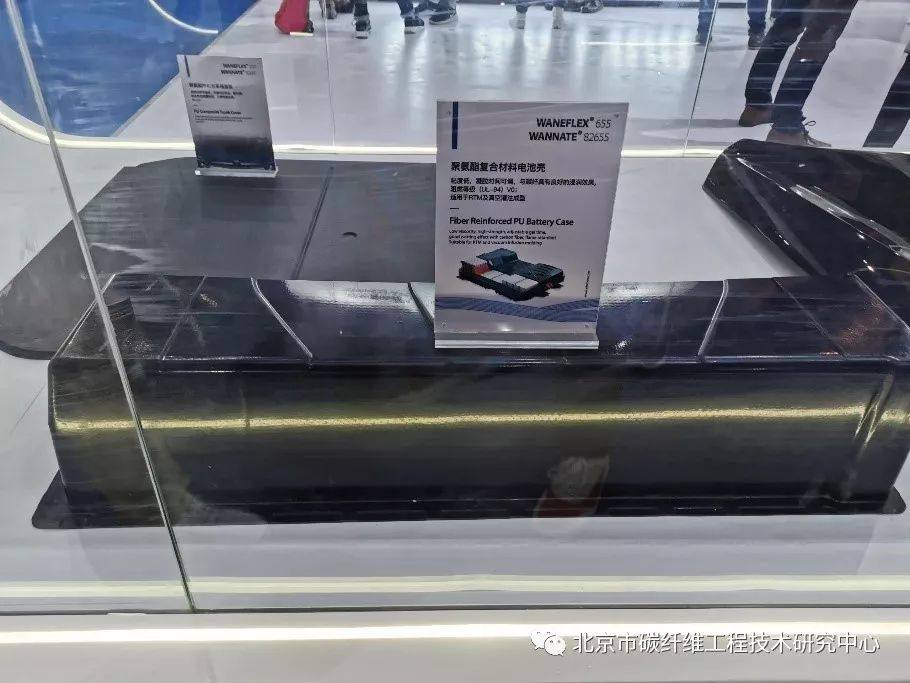
图5. 国内开发并批量供货的某款HP-RTM工艺电池包
(图片来源: 拍摄自2019年中国国际复合材料工业技术展览会)
3.快速预浸料模压(R-PCM)工艺
R-PCM工艺,以传统预浸料模压工艺为基础,通过引入快速固化树脂体系的预浸料、模外预成型减少占模时间、主辅装备的自动化配合生产,使其达到汽车零部件量产节拍。

图6. 快速预浸料模压工艺过程
(图片来源: Mitsubishi Rayon Co.,Ltd.)
快速预浸料模压工艺先将预浸料按照需求裁切下料成预浸料堆叠,在加热后,通过冷压的方式进行预成型,得到预制体,再将预制体进行模压成型,树脂完全固化后,开模取出产品即完成一个节拍的制造。
对于电池箱上盖产品来说,因铺层层数较少,在z向棱边处不宜采用整体搭接的铺层方式,通常额外采用局部补强方案,以免产生过多的性能损失。在电池箱上下盖安装的法兰边处,同样也应采取局部补强方案,避免螺接安装时法兰边压溃失效。上述铺层及补强的要点均通过预成型阶段实现,以避免延长模压成型的占模时间,从而保证产品的生产节拍。预浸料采用高模连续玻纤和改性树脂的方案,能够保证产品的力学性能、阻燃、绝缘、密封、使用温度等要求。现阶段,各主机厂和电池包厂家也将快速预浸料模压方案作为电池箱轻量化的其中一个研究方向。
对于这三种工艺路径,根据其自身的特点,对比如下:
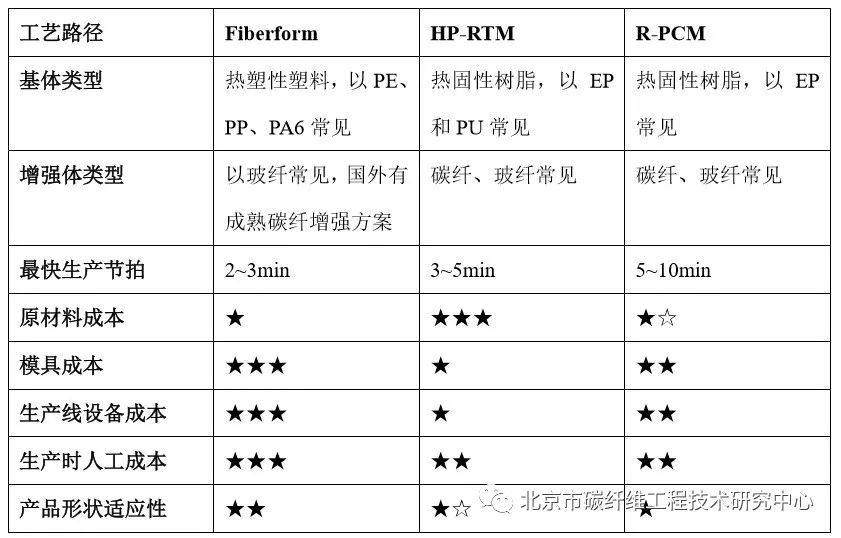
表1. 三种工艺路径的对比
①上述对比为作者根据自身经验编写,由于技术背景不同,对于这三种工艺路径的理解可能因人而异;
②上述对比中“★”和“☆”的数量多代表某工艺路径在这一项对比的表现更优。“★”和“☆”分别代表“一颗星”和“半颗星”。
长
按
关
注
北京市碳纤维工程技术研究中心
ID : bjlxcf
服务热线:010-61438919
地址:北京市顺义区安祥大街5号
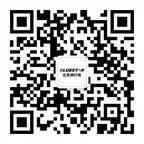
原文始发于微信公众号(北京市碳纤维工程技术研究中心):【技术交流—工艺】连续纤维增强复合材料轻量化动力电池箱上壳体的常见工艺路径
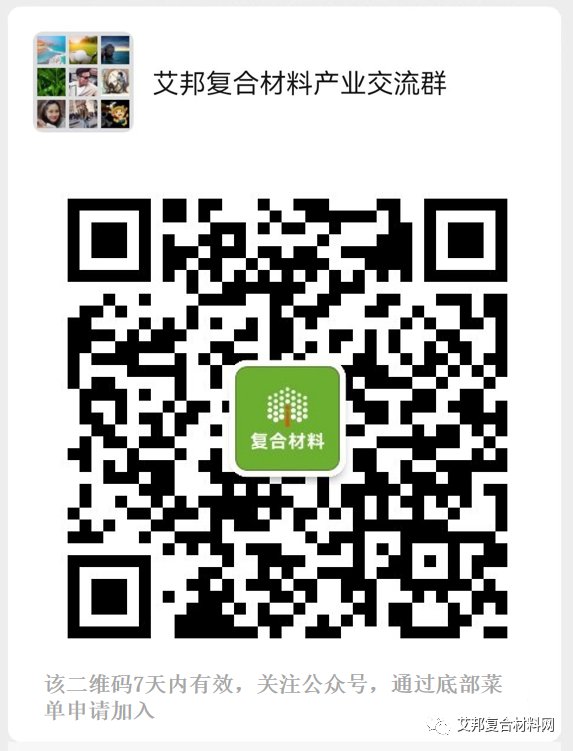