//带你看电池包结构轻量化
”
动力电池包是电动汽车核心零部件之一,电池包重量约占整车总重20-30%,也是整车生产中成本占比最高的部件之一。
众所周知,电池包对于安全性的要求非常之严苛,同时也决定了整车在功率和续航里程上的表现。
想要提升性能,车身整体的重量也至关重要。其中重量占到将近三分之一的电池包轻量化问题也成为了关键。
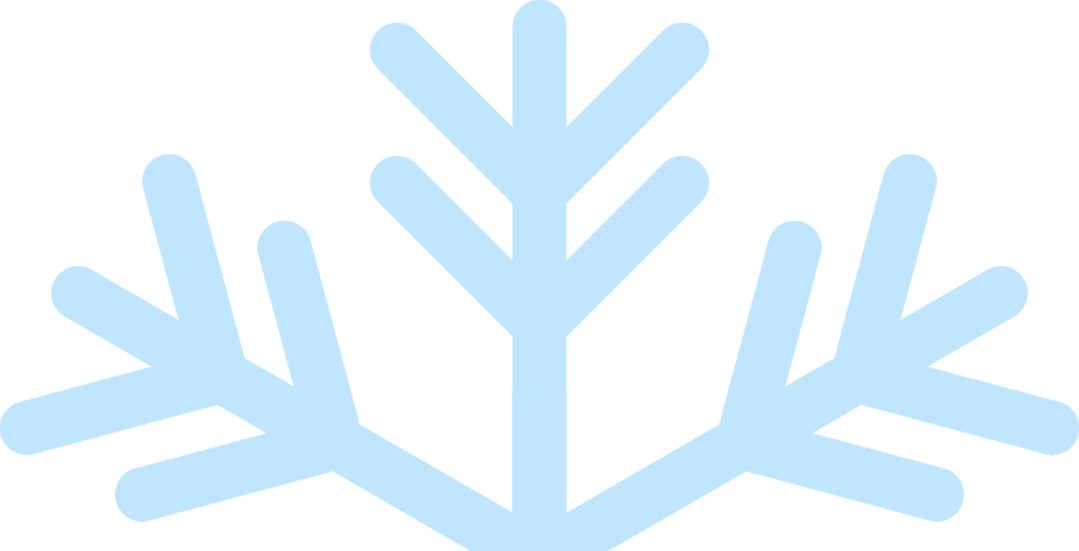
电池包为什么要轻量化?
研究数据表明,传统燃油汽车减重10%,经济性可提升6-8%;
而等速行驶工况下,电动汽车自重降低10%,可使整车增加10%左右的续驶里程。
那么如何提升续航里程呢?
从电池包的角度来看,由于电芯材料组分和尺寸上的限制较大,所以想要减重就只能从结构上下手,箱体轻量化和模组紧凑化成为了当下新能源车企研究的重点方向。
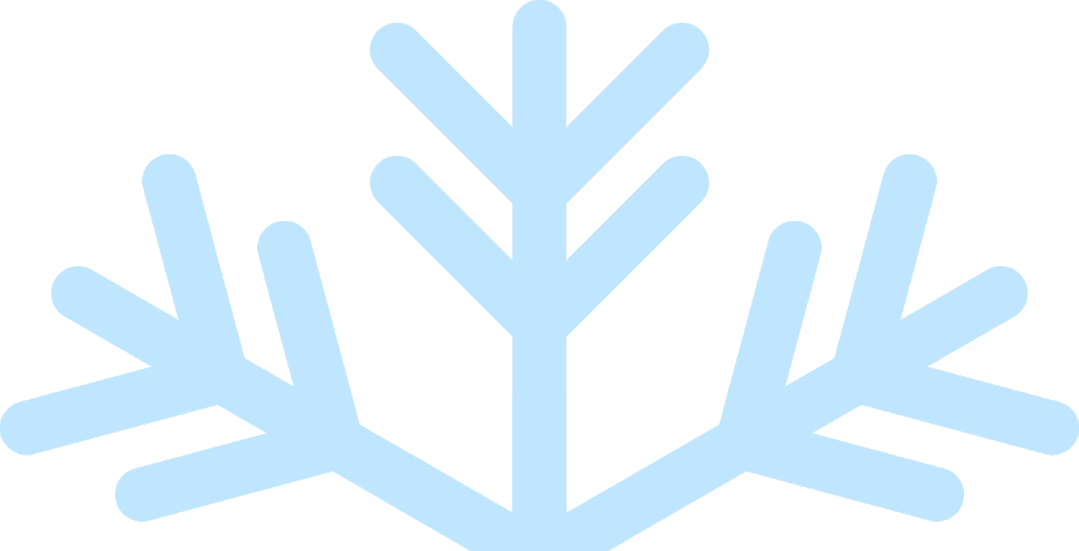
如何实现电池包轻量化?
电池包的轻量化大致可以分为两大层面——系统设计层面和详细设计层面。具体细分层级可见下图:
轻量化之余,电池包的结构还依然需要满足机械安全、密封绝缘和防火等安全需求。箱体结构的强度、刚度、耐撞性、稳定性都会对电池包性能产生影响。
轻量化之路中,较为有效的方式有以下5大方法:
// 01 优化电池包布置方式
”
在电池包箱体有限空间内,一定数量电池单体通过特定机械连接和电连接组成电池模组。
根据车用电池包的空间形状与承载特点,电池模组串并联排布组成动力电池系统,电池包中模组布置和结构形式差异较大。
电池单体常用类型有圆柱形、方形铝壳和软包铝塑膜等,此外电池包内部还布置有BMS控制器、高压线束等辅助功能部件。
电池包结构构成
电池包内部功能件
动力电池包的布置形式通常由整车空间特征决定,需考虑车辆驱动方式、整车重心位置与离地间隙等因素。
动力电池包生产企业根据整车企业需求,开发出模组排布不同、电池包箱体形状和安装吊耳位置各异的车用动力电池包。
经过不断研究与发展,电池包常用结构布置形式有车身底部悬置式、车身结构一体式和标准箱体分布式等。
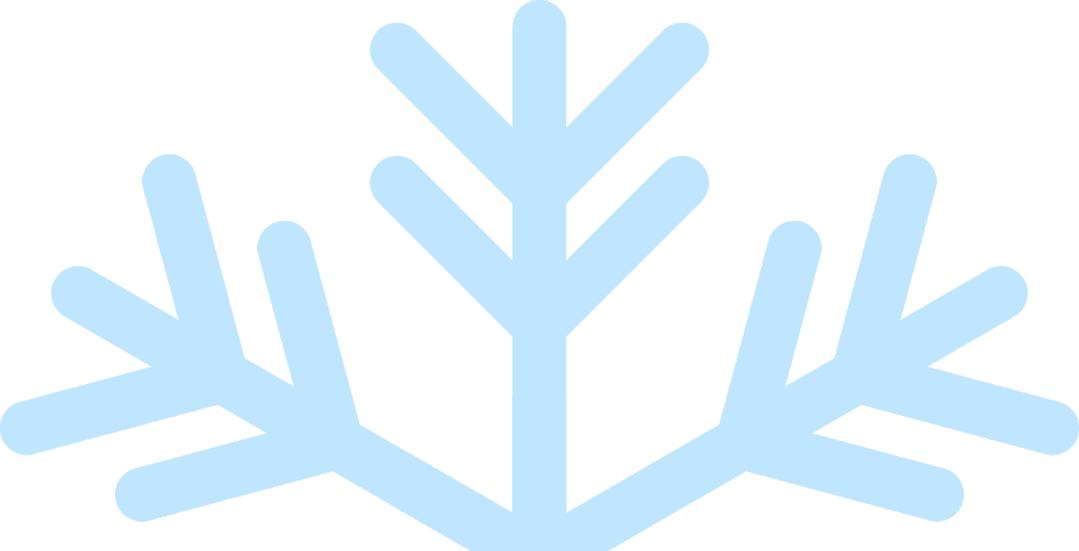
车身底部悬置式
早期电动汽车多由传统燃油车改装而成,动力电池包通常安装在汽车前舱、后备箱、地板底部等位置,如下图所示的日产Leaf“凹”形电池包。
日产Leaf 电池包
车身底部悬置式电池包采用螺栓连接于汽车车架底部,具有设计高效灵活、生产制造独立性好等优点,是乘用车广泛采用的动力电池包结构形式,如日产Leaf、吉利帝豪EV等车型。
吉利 帝豪EV Pro
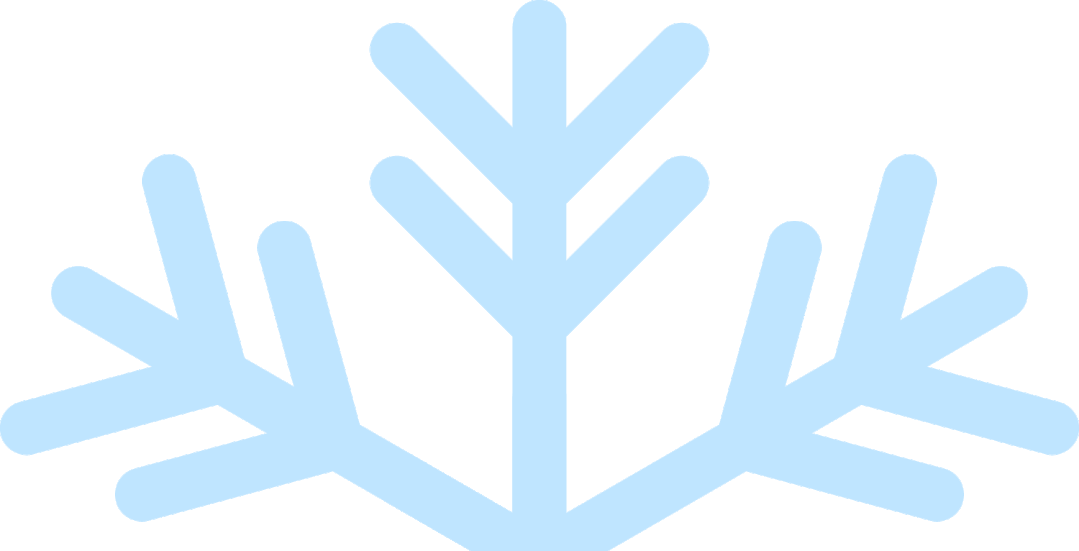
箱体分布式
标准箱体分布式是通过几个相同或者结构近似的标准箱体电池包串并联形成电池系统,具有布置灵活,安装位置多样等特点。
空间较大且规整的客车或专用汽车多采用该种结构形式,如宇通E10 纯电动客车等。
标准箱体电池包
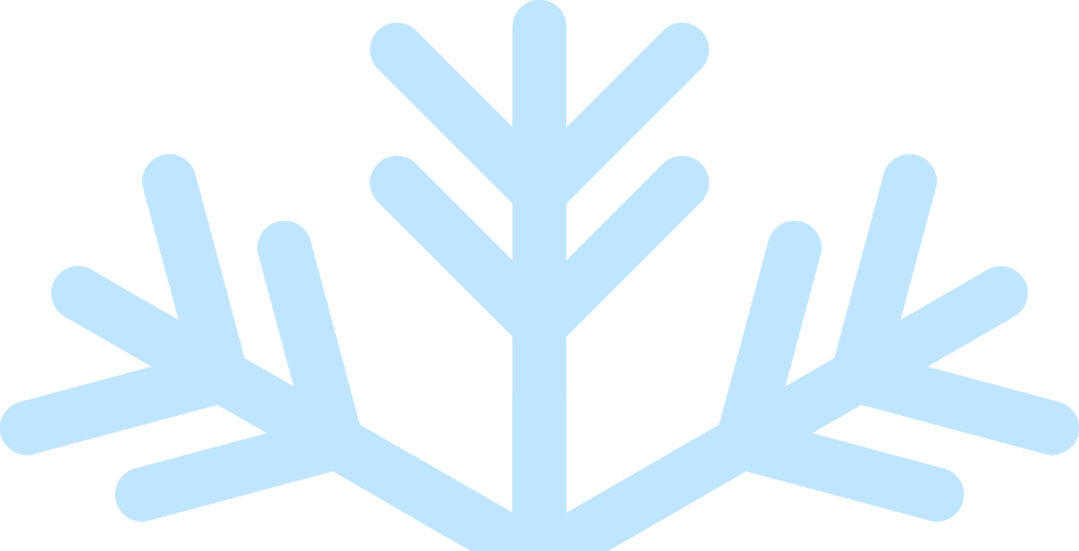
车身结构一体式
随着电动汽车续航里程的需求不断提高,空间受限的传统汽车结构无法满足最优设计要求,车身结构一体式电池包结构布置形式逐渐受到重视。
电动汽车正向设计技术的成熟使得电动汽车专用设计平台出现,如图所示的广汽GEB电动汽车专用设计平台,就将电池包融合至车身结构中。
广汽GEB平台
电动汽车续驶里程需求增加,外加汽车正向设计技术的发展,促使车身设计与电池包结构协同开发,力求车身结构紧凑同时电池包性能较优。
当下,平台化、模块化的车身结构一体式动力电池包逐渐增多,如搭载大众MEB平台的奥迪Q4 e-tron、特斯拉TESLA平台设计的Model S和Model X等车型。
// 02 优化电池模组
”
系统设计层面下,电池包轻量化设计首先从电芯参数和单体尺寸选择开始。
不同化学体系与尺寸参数下锂离子动力电芯与动力电池系统存在匹配设计问题,通常需在电池系统概念设计阶段计算确定。
最后则是通过优化电池包箱体内部布置、减少设计层级,实现箱体空间最大利用率。
例如宁德时代提出的无模组设计技术(Cell To Pack,CTP),图为宁德时代某CTP系统结构设计。
宁德时代CTP设计应用实例
该CTP设计中,采用了单体和电池管理系统直接固定在电池包壳体中,电芯内置在上下壳体中,壳体内部填充导热胶。
此外,电芯侧壁和电芯壳体间内置压力或者温度传感器,两种传感器协同作用下能够排查不良电芯单体,并且提前探测到电芯可能发生热失控等安全事故。
该设计形式由于不采用模组结构,使电池包体积利用率提升了15-20%;电芯单独装配,降低装配难度,提高生产效率约50%;
更为重要的是,可实现故障电芯的及时检测与更换,电芯壳体加强方案可降低电池包外壳的防护等级。
// 03 新型成组方式
”
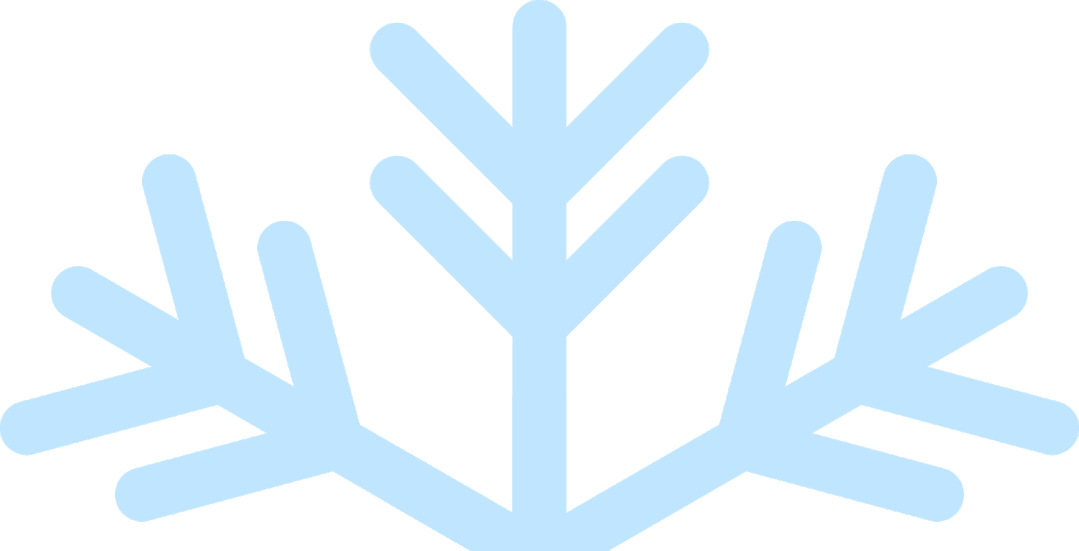
大模块设计
将单体电芯的尺寸和容量增加,致使每个单体电芯分摊的结构件质量减少。例如宁德时代的大模组设计结构:
CATL大模组设计实例
通过大模组设计取消了现有技术中的电池箱体,直接将电池模组通过固定件穿过支撑套筒与安装梁安装在整车上,实现电池包轻量化同时提高了电池包在整车上连接强度。
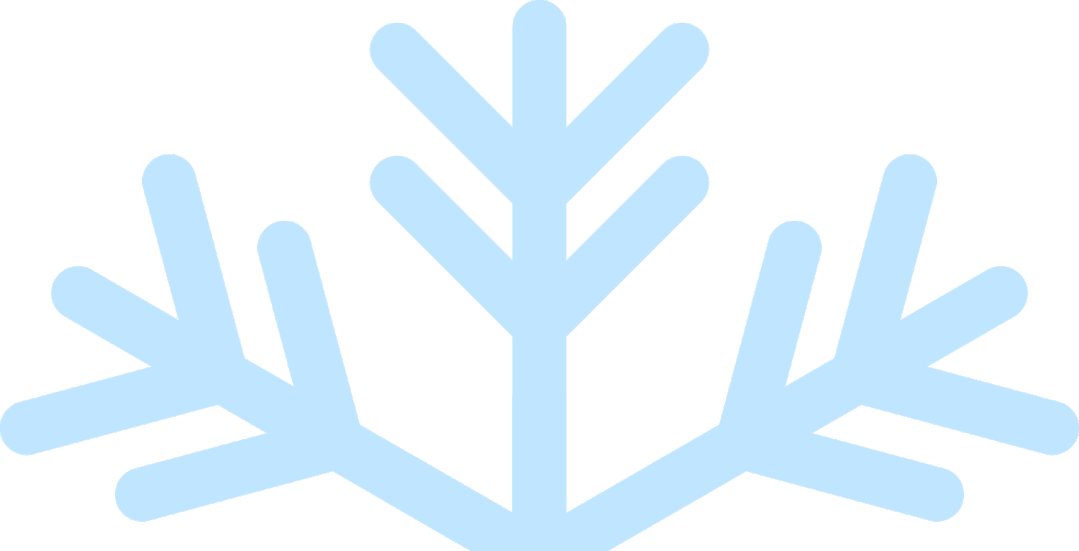
一体化设计
减少电池包模组等中间层级,将单体电芯尺寸做到最佳,提高箱体空间利用率。
例如比亚迪的“刀片电池”电池包设计方案,如图所示,通过设计出一种扁平化大尺寸电芯,采用阵列排布方式布置于电池包箱体内部,单体电池就像“刀片”一样插入到电池包中。
比亚迪刀片电池结构
据悉,该设计能使电池包比能量提升50%左右,生产成本降低约30%。
// 04 轻质材料应用
”
来到今天的重头戏——材料轻量化。
为什么说是“重”头戏呢?因为箱体减重设计中,运用轻质材料对箱体整体减重的效果非常明显。
目前应用较为成熟的轻质材料是铝镁合金和复合材料两大类。
金属类材料中,铝合金除了重量轻、抗氧好之外,还有利于回收,在电池包上的应用量非常大。
考虑到结构强度,压铸铝箱和挤压-拼焊铝箱多用在下箱体,冲压-拼焊铝箱一般用在上箱盖。
铝合金在电池包中的应用
来到非金属材料这边,复合材料可谓是目前的大热门。它所具备的重量极轻、绝缘性能好、加工成型简便的优势在电池包乃至整车上都发扬光大。
目前诸如发动机罩、油底壳、电池包上箱盖等领域中,各种复合材料制成的零部件正在大规模替代传统金属零部件。
复合材料在电池包中的应用
但也要注意,复合材料受制于原料、成本等方面的限制,目前应用比较多的有玻纤增强塑料(SMC),以及各类改性树脂。
数据显示,SMC制成的电池包上箱盖比传统金属材料上盖减重约为38%,碳纤维复合材料应用也在逐渐增多,复合材料减重效果明显。
有部分企业尝试将复合材料应用在电动汽车下底板,但复合材料刚度特性较差,需要加厚尺寸或者采用夹层结构来提升结构的抗弯特性。
同时会在电池包下箱体设计成夹层结构,并在中间层增加金属或者蜂窝铝结构,将金属与非金属结合,具有轻质高强、耐撞性好等诸多优点。
下表例举了各种轻质材料的性能参数及特点:
镁铝合金、复合材料等轻质材料在电池包结构轻量化设计中减重效果显著,但目前轻质材料应用在电池包结构设计中存在以下2点不足:
-
结合电池包关键性能开发出性能和轻量化效果均优的电池包结构欠缺,可借鉴的研究成果、设计方法不多;
-
合适的材料用在合适的位置在电池包结构设计中已有初步应用,但对电池包多材料选型方法,结合性能约束的多材料设计方法研究不足。
// 05 极限设计
”
极限设计是指在产品详细设计阶段进行性能优化或后期对产品进行设计改良。
极限设计需清楚设计的临界值,不仅要满足各项性能要求,还需满足零部件加工、产品装配工艺要求。
极限设计通常借助CAE对产品各项性能临界值和生产工艺参数探索,通过CAE仿真分析技术精准定位。
例如将电池包箱体承载部位加强设计,而非承重部位使用薄壁材料,箱体不同位置变厚度实现结构性能满足设计要求又尽可能减重。
铝制箱体结构极限设计实例
除了这些轻量化的需求以外,当下汽车工业的发展对塑料提出了更多 的需求和挑战。
一 END 一
来源:《车用动力电池包多材料结构优化与轻量化设计》、汽车材料网
编辑:FAN | 审核:HOHO
原文始发于微信公众号(新材料产业圈):电池包轻量化的5种关键方法
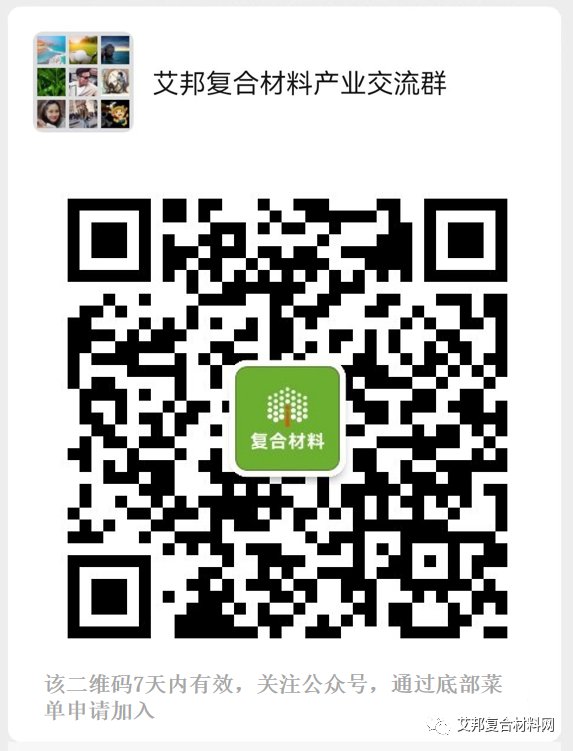