温馨提示:如果您是高分子行业相关产业链,如塑料,弹性体,橡胶,注塑、挤出、模具,鞋材,3D打印耗材,塑料包装,汽车塑料,PP、PE、钙粉,白油,抗氧剂等助剂行业从业者,请点击标题下面的“艾邦高分子”进行关注; 中国高分子论坛BBS.POLYTPE.COM;平台覆盖行业5万专业用户!投稿邮箱:polytpe@qq.com,小编微信:18666186648 |
1、汽车工业的现状
作为世界上最大的工业领域,2010年的汽车行业的工业产值达到9000亿欧元,销售车辆5500-6000万辆。
按照车辆销售价格,分成四个不同级别:豪华车、高端车、中级车和入门级车辆。目前的销售价格,豪华车>7.5万欧元,高端车>2.5万欧元,中级车>1.5万欧元,入门车<1万欧元。
按照区域主要分成西欧,东欧,北美,拉丁美洲,日本和其他亚洲国家等。
豪华车的品牌有劳斯莱斯、宾利、法拉利、阿斯顿-马丁、BMW7系和8系、梅赛德斯S系列、奥迪A8等。
高端车品牌有BMW、梅赛德斯、Audi等。豪华车和高端车具有全球性市场的特点,通常在产地国生产,全球市场销售。
中级车和入门级车辆具有很强的区域性,一般采用本土化生产,设计和品牌推广也是主要针对本土开展。
在中国,中低端品牌有国产奇瑞、上汽等,属于区域性的品牌。Tata在印度处于领先地位,而在其他地区,市场就很有限。但是西方的中级车品牌,例如大众、GM、PSA在新兴市场占据很重要的位置,销售也在不断增加,但在低端市场,往往比不上本土竞争对手。
近几年,全球汽车工业的发展主要源于新兴市场产量的激增,尤其是中国。中国不再简单的作为西方的世界工厂,过去取得的经济成就也带动了国内消费和服务业的兴起。汽车消费的发展就是一个强有力的佐证。世界上,几乎所有的汽车公司都在中国开设了本土工厂,这些合资工厂并非为了降低西方消费者的成本,而是为了满足中国消费者对汽车的需求。
汽车工业的发展,曾经是西方战后的经济恢复的象征,如今也成为中国等新兴国家经济实力的表现。预计,到了2015年,世界上每两部汽车,就有一部在亚洲制造,即使不包括日本。中国生产的汽车比北美、日本和德国加起来的产量还要多。
2. 60年来汽车复合材料发展缓慢
复合材料在汽车领域已经有了一段很长的历史,可以追溯到1950s,主要用于汽车非结构部件,例如硬质车顶。从70/80年代开始,越来越多的采用热塑性复合材料生产汽车内饰以及用热固性复合材料制造次结构件,例如保险杠的梁。由于复合材料具有很多优点,如:设计灵活、容易成型、轻质、耐腐蚀等,虽然原材料和工艺成本高于钢材和铝,在汽车领域还是获得了一些应用。喷漆以后钢汽车部件的成本大约是3-4欧元/公斤,复合材料次结构件的成本大约是8-10欧元/公斤。
汽车复合材料已经不再是一个小众市场。相对于复合材料的其他应用领域,汽车领域已经是其最大市场,大约占体积的20%,销售额的18%。如今,世界平均每辆乘用车,复合材料约占总重量的6%。具体随汽车的级别、地区和部件有所不同。对于所有级别的车辆,仪表板等内饰件,75%的车辆采用了复合材料,但是对于结构部件,仅仅在高端车型中有所应用。例如汽车的底盘,只有豪华车中的10%左右采用了复合材料。总的来说,复合材料的用量豪华车大约是15%,高端车大约9%,中级车6%,入门级车辆4%。另外,对于新兴市场中级车和入门级车辆,复合材料的用量通常比发达国家市场同级别车型低1%。最近,复合材料的回收越来越引起人们的关注。热固性复合材料比热塑性相比,回收的难度要大很多。所以,在现有的复合材料应用的基础上,有采用热塑性取代热固性树脂体系的趋势。
图1 复合材料在汽车领域的应用从1980s开始加速
3. 2010年-2015年的趋势
近期,汽车整车厂对复合材料的兴趣不断增加。这主要源于不断严格的排放法规(将来CO2排放超标罚款)以及增加的燃油成本,这些都可以通过复合材料轻量化来实现。复合材料可以减轻重量,进而降低碳排放,抵消增加的材料费用和工艺成本。
欧洲议会2013年4月24日通过一项法律草案,要求到2020年在欧盟出售的新汽车平均每公里二氧化碳排放量由目前的130克减少到95克。对于那些计划生产二氧化碳排放量超标车的欧盟厂商,草案提出了补救措施,即这些厂商必须同时生产每公里二氧化碳排放量不足50克的超清洁汽车。具体规定如下:2013年至2015年每生产1辆这样的超清洁汽车,最多可生产3.5辆超标车;2016年至2023年可生产1.5辆超标车;2024年以后可生产1辆超标车。
尽管整车厂对复合材料的兴趣有所增加,但是减少碳排放和燃油消耗的方法不仅仅是车辆减重。最经济的方法是提高燃油利用率,这可能是整车厂的首选,特别是对于中级车和入门级车辆,因为这两个级别的车辆,发动机排量常常不是购买的主要考虑因素。对于现有复合材料和金属在成本上的差距,需要一段时间,通过技术进步来弥补。例如,对于底盘这样的结构部件,加工好的钢结构的成本大约是3-4欧元/公斤,但是碳纤维环氧复合材料结构的成本(基于现有材料和工艺技术)高于30欧元/公斤。
不同的整车厂家最终会获得不同的解决方案,这些方案能够达成目标的程度也会有所差异。总的来看,汽车复合材料用量的增加,主要集中在量产车车身的三个领域:汽车底盘,车身覆盖件和次结构部件。这三个方面可以大幅度的提高汽车复合材料的用量。底盘的重量约占总重量的25%,是最具减重效率的部件。但是,按照预计,量产车领域的汽车复合材料用量的突破不会在2015年以前出现。在2015年前的这段时间,汽车复合材料部件的用量会有少量增加,成本会有所降低,复合材料制造厂家和整车厂对复合材料的材料和工艺进一步熟悉;同时,复合材料开始用于一些高端车型的旗舰项目,例如德国的BMW的i3、美国的Telsa电动汽车以及英国的Axon插电式混合动力汽车。
到2015年,汽车复合材料的用量会达到200万吨,增长主要来源于汽车产业的自然增长(年产量增加6%)和已经采用了复合材料的汽车部件的市场份额的增加。
4.2015-2020年的趋势
2015年以后,随着碳排放法规(2020年生效,并逐步严格)的临近,碳纤维成本的降低以及快速固化环氧树脂的出现,加上工艺和自动化设备的不断成熟,例如针对热固性复合材料快速制造开发的HP RTM(高压树脂转移模塑)工艺和热塑性复合材料层板热成型自动化设备的研发,到2020年,碳纤维复合材料的综合性价比会优于金属,取代金属材料,用于量产车的底盘制造,并涵盖大多数的高端车型和少量的中级车。下面分别对HP RTM工艺和热塑性层板的解决方案做详细介绍。
图2 不同级别的汽车不同部件汽车复合材料的应用率
5.热固性复合材料高压RTM工艺
航空工业采用树脂传递模塑成型工艺(RTM),进行大型高强度结构件的生产,降低工艺成本。在汽车的制造过程中,也有采用RTM工艺进行零部件的生产,主要目的是为了达到更好的表面质量,但是只用于小批量生产的顶级轿车中。
图3 不用树脂转移模塑工艺的图解
通常RTM工艺的注射压力是 6-15bar最大不超过20bar,工艺周期大约1小时。但是高压RTM工艺,注射压力在10-60bar,工艺周期大约6分钟。
目前世界上,高压RTM工艺的设备厂家有:德国Dieffenbacher+ KraussMaffei;德国Schuller + Frimo和意大利的Cannon S.p.A公司,一般采用的两家公司合作的方式。下面主要就Dieffenbacher+ KraussMaffei的情况做具体的介绍,其他厂家的设备大同小异。
德国加工机械领域的专家迪芬巴赫公司(Dieffenbacher)和克劳斯玛菲公司(KraussMaffei)共同开发了高压树脂传递模塑成型工艺(HP-RTM)的自动化生产线。这条生产系统包括预成型加工、压制过程,以及修整工艺。相比于传统的RTM工艺,HP-RTM工艺减少了树脂注射次数,提高了预制件的浸渍质量,并缩短了成型周期。
(1)预制件过程
对于HP-RTM部件的生产,需要制造一个由织物增强材料制成的预制件。这样的预制件在迪芬巴赫的预成型中心制造完成,通常使用一个完全自动化的过程。
图5 高压RTM工艺的自动化过程
由碳纤或玻纤制成柔软的纤维织物或纤维毡从卷轴上开卷后放入切割机。使用CNC切割技术,纤维铺层被切割成部件加工所需尺寸。该过程通过由现有的CAD零件参数得到的切割程序完成。切割成形的纤维铺层材料层合到一起,然后放置到成型单元中。可以使用机器人来可靠地处理切割织物、纤维毡,以及预制件。预制件成型中心可以作为一个单独的单元来运行,也可与压制工艺一起结合在产线上。
(2)合模加压过程
预制件的加工过程之后就是合模加压。在合模加压的过程中,环氧树脂系统浸渍预制件,以及其固化。
在用机器人将预制件放置到RTM模具中之后,根据模内压力及部件的尺寸和复杂性,采用一台迪芬巴赫液压压机用高达36000 kN(3600 t)的压力完成实际的合模加压过程。压机在很短的建压时间内达到450 mm/s的合模速度和40 mm/s的加压速度。迪芬巴赫短冲程系统能够确保压机具有非常高的能效,尤其具有很短的成型时间和较大的滑块行程。与传统的合模加压技术相比,可以提高50%的能效。
合模加压控制系统允许使用不同的操作程序,并能缩短生产周期。模座周期性地进入和离开压机,只需要很短的换模式时间、装卸过程,以及生产线下对下半模的清洁。完成高压注射过程后,还可以通过再加压来获得部件质量的改善。
(3)注射过程
将低粘度的反应性混合物注入到闭模中浸渍预制件。通过使用克劳斯玛菲的技术,能够使注射速度达到10-200 g/s,取决于树脂系统以及部件的尺寸和工艺设计。在一个闭环过程中,对树脂和固化剂进行精确计量,并在高压下进行混合,得到反应性混合物。
高压计量使得注射时间更短,并提高预制件的浸润度,因而能以较短的固化时间来处理树脂系统。这带来了更短的生产周期和更高的成本效益。此外,这还提供了额外的好处,比如,能在保持出色的表面品质的同时获得更低的孔隙度。而对温度的精确控制则能进一步缩短加工周期,并从特殊RTM树脂体系中获益。
克劳斯玛菲的高压混合头消除了耗费成本的停工时间,也无需使用清洗传统低压混合头时所需的特殊材料。这种混合头具有自清洁能力,因此能在大批量生产时表现出突出的能效优势,它的这种优势已经在多种量化生产中得到了验证。
通过脱模剂供料块,能够将工艺所需的脱模剂直接引入紧凑的自清洁克劳斯玛菲高压混合头,并且,即使在最低剂量(如0.1 g/sec)时,仍具有极高的准确性和工艺可靠性。具有高精度、高重复性的脱模剂计量对于可靠地实施下游工艺来说无疑是非常必要的。
(4)修整
修整是工艺链最后步骤的其中一环。包括部件的外廓修边,增加安装孔和嵌件开孔。用铣刀进行的修整采用的由克劳斯玛菲开发的定制化解决方案。可以采用自动化切割台或手提式切割机。工具的选择主要取决于部件的尺寸和复杂程度。机器人被用于在工艺步骤之间进行零部件的处理。
图6 复合材料部件的修整
6.热塑性复合材料汽车应用
这几年,在复合材料领域,热塑性复合材料也备受关注。
(1)有机板混合结构包覆成型工艺
未来两年内,复合材料有机板(Organosheet)混合结构技术将在汽车结构部件的量产化应用中实现突破。目前,至少有两家材料供应商,即巴斯夫和朗盛,以及两家机器供应商,即恩格尔和克劳斯玛菲,正走在该技术开发的最前沿。
如果您对以上材料熟悉,诚邀您加入汽车塑料微信群,请加群主:18666186648,注明”汽车“
采用全塑料的“有机板混合结构”取代汽车中的塑料-金属的“混合”结构。新的工艺直接在连续板材的基础上,预成型,然后包覆成型,代替过去在金属预成型件的基础上通过包覆成型,加上加强筋。恩格尔和克劳斯玛菲都是采用尼龙6热塑性树脂层纤维织物压板(热成型),在加上尼龙6(加或者不加纤维增强),包覆成型。材料厂家是德国Bond-Laminates的Tepex有机板,以及朗盛的尼龙包覆成型颗粒料。恩格尔称之为:Organomelt工艺,克劳斯玛菲则称之为FiberForm工艺。包覆成型的混合结构工艺不仅仅可以对热塑性适用,也可以用于热固性的复合材料混合部件,参见图7。
“有机板(Organosheet)”的混合结构部件成型工艺的生产流程是:首先加热一个用PA6连续纤维增强有机板,然后将其放入注塑模具中,热成型出一个三维形状,并用另外的PA6树脂(未填充的或者是玻璃纤维增强的)对其进行包覆成型。在某些情况下,在将板坯放入注塑模具中前,先对其进行热成型。
如果采用热塑性复合材料混合结构,主要市场将是汽车内饰,包括座椅部分的组件、门侧防撞梁、汽车横向悬架梁、刹车踏板、转向柱支架、安全气囊组件和前端组件等。如果改成热固性的复合材料混合结构,可以用于结构件或者次结构件。但是,目前国外还很少有针对汽车领域的热固性的复合材料混合结构包覆成型的研究和应用。
汽车塑料微信群请加群主:18666186648,注明”汽车“
在K 2010展会中,恩格尔和克劳斯玛菲这两家公司都第一次在两个复杂的成型单元中证明了这项技术。当时,恩格尔成型了一个转向柱支架,而克劳斯玛菲则成型了一个门侧防撞梁。两家公司均采用了德国Bond-Laminates公司(最近已被朗盛收购)提供的Tepex复合材料板材,并采用朗盛的尼龙材料对该组件进行包覆成型。将有机板放到300℃的加热炉中预热30~40s,然后将加热后的板材送入注塑模具中。闭合模具,对该板材进行预成型, 接着从其上方将另外的尼龙材料注入到特定区域。按加热炉能力的不同,整个循环时间从33s到55s。
图8 热塑性复合材料混合结构转向柱支架
(2)热塑性树脂传递模塑成型工艺
作为热塑性复合材料技术的下一发展目标,己内酰胺单体在模内聚合为PA6的技术正在推进之中。该技术允许采用低黏度的己内酰胺浸润放于模具中的干纤维,经反应后可在线形成一种尼龙基的复合材料。
巴斯夫与西格里集团正在联合开发一种基于反应性尼龙系统和碳纤维的复合材料,以实现热塑性复合材料的低成本生产。该材料体系是为T-RTM工艺(热塑性树脂传递模塑成型工艺)以及反应注射成型工艺而准备的,以获得比传统热固性RTM工艺更短的生产循环时间。为适应这些更快速加工技术的要求而对材料系统的调整,将在采用碳纤维复合材料制成的结构部件进入汽车量产化应用的过程中发挥重要作用。己内酰胺在线聚合为尼龙6的机器系统正由恩格尔在进行开发。
7.结论
汽车复合材料的发展,结合了化工、机械制造以及汽车复合材料设计,从经济结构来看,最新突破应该源于德国。德国的工业结构结合了大多数的豪华汽车和高端车,另外朗盛、巴斯夫等世界顶级化工企业以及精密的机械制造厂家,例如迪芬巴赫公司和克劳斯玛菲等。随着碳排放法规的不断临近,复合材料在汽车行业的突破会在2015年以后时间,欧洲汽车行业也会是先进材料的倡导者和先行者。热塑性复合材料和热固性复合材料不存在谁替代谁的问题,因为他们的各方面的性能都有所差异,快速成型和自动化都是共同的发展方向。最终汽车结构的优化一定是和金属类似,建立在多材料体系基础上的混合结构,例如包覆模塑工艺成型的部件。
参考文献:
JEC Composites: composites penetration growth in automotive towards mass production 2010-2020 trends and forecasts
‘ORGANIC HYBRID’ COMPOSITES HIGHLIGHTED AT K SHOW:
http://www.ptonline.com/articles/organic-hybrid-composites-highlighted-at-k-show
THE NEW LIGHTWEIGHTS: INJECTION MOLDED 'HYBRID' COMPOSITES SPUR AUTOMOTIVE INNOVATION http://www.ptonline.com/articles/the-new-lightweights-injection-molded-hybrid-composites-spur-automotive-innovation
HP-RTM技术用于汽车轻量化设计
http://cn.industrysourcing.com/articles/256885.aspx
(来源: SAMPE)
推荐阅读:请阅读原文链接进入阅读,或者回复关键词“汽车”
汽车用塑料
聚碳酸酯和聚碳酸酯共混物材料助力电动汽车充电行业
解密汽车内饰材料碳纤维和塑料内饰
PBT工程塑料在汽车领域的应用
改性塑料在汽车轻量化上发挥大作用
汽车用热熔胶类型及应用举例
巴斯夫告诉您热塑性弹性体TPU在汽车包胶上的应用
热塑性弹性体在汽车行业应用的优势
[动态]杜邦亮相德国K展针对汽车行业推出新型弹性体
[汽车]TPE用于汽车可剥性的保护膜
TPE在汽车行业的应用以及趋势报告(中国热塑性弹性体论坛2013年版)
TPC是什么?汽车用热塑性弹性体介绍
热塑性弹性体在汽车行业的应用进展
专业解读:特斯拉等汽车充电桩给高分子以及TPE产业带来什么?
汽车检测
【图】专业介绍汽车VOC测试
全球汽车制造商测试塑料的VOC排放
新技术
塑料汽车应用值得关注的25个技术
首款3D打印汽车采用SABIC材料
汽车行业动态
全球十大汽车配件供应商,中国2家上榜!
2014年中国十大汽车模具公司排名
其他
【转】汽车行业通用标准采购流程,知己知彼!
63个汽车基本故障以及排除方法
以上文章请阅读原文链接进入阅读
↓↓↓
原文始发于微信公众号(艾邦高分子):汽车复合材料的回顾和展望
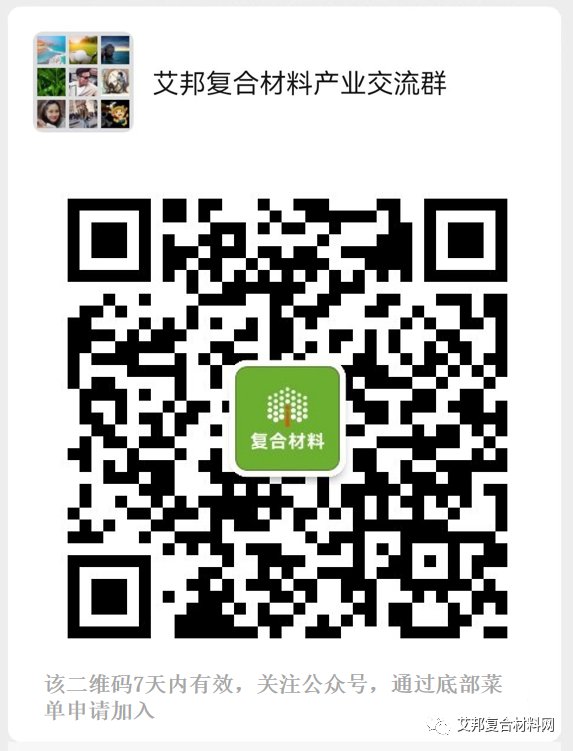