摘要:以CF/PEEK和CF/PEKK热塑性复合材料为研究对象,对其适用的低成本模压成型、自动铺丝结合模压两步法原位成型工艺进行初步探索,并对两种热塑性复合材料体系的基本特性、成型质量与性能进行对比分析。首先采用幅宽305mm的CF/PEKK体系开展模压成型工艺研究,发现冷却速率对短梁强度影响不大,而成型压力对短梁强度有一定影响,在成型压力2.0MPa、成型温度370℃、冷却速率–15℃/min工艺条件下其短梁强度达到(135.65±4.72)MPa,纤维含量达到61.8%,成型质量良好。同时对于6.35mm宽CF/PEEK窄带,初步探索其自动铺丝结合模压两步法原位成型工艺,发现与模压成型CF/PEKK同等工艺条件下,所得CF/PEEK层合板成型质量良好,破坏模式与CF/PEKK体系相近,但是短梁强度较低,微观破坏行为有一定差异。研究结果可为热塑性复合材料应用于航空主承力结构的材料和工艺选择提供基础数据和技术参考。
本文采用的原材料及主要仪器设备厂家和型号规格如表1所示。
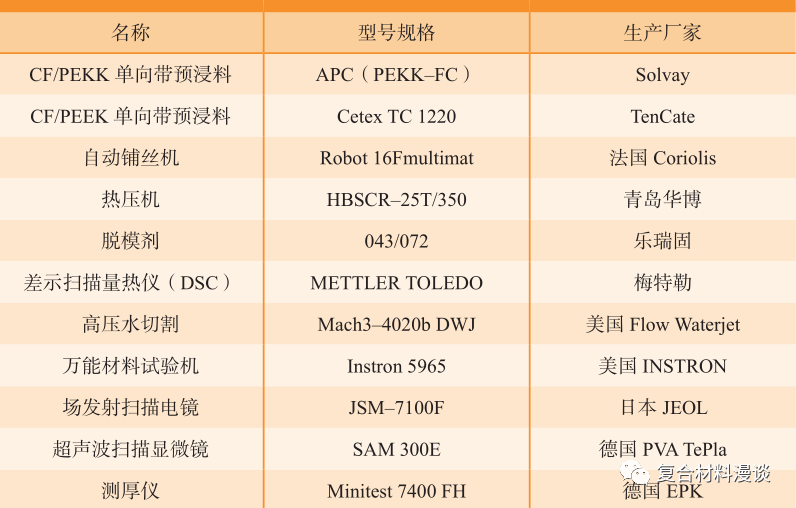
本文采用模压成型工艺制备CF/PEKK热塑性复合材料层合板,主要包括铺放准备、铺放、预热、成型、冷却脱模及机加检测等步骤,其工艺流程如图1所示。
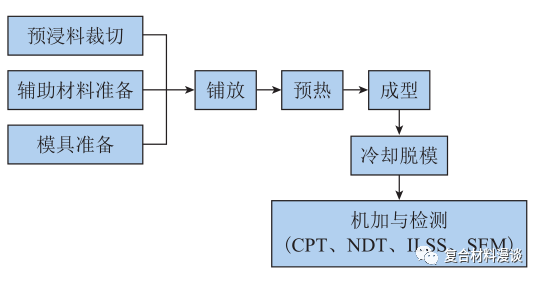
首先进行预浸料裁切和辅助材料准备,同时进行模具清理和准备;之后将预浸料按设计好的铺层方式进行铺层,采用单向铺层,尺寸是150mm×100mm;最后进行合模,并将工装转移至热压机设置成型工艺制度进行固结成型。典型热压工艺制度为340℃预热,升温至370℃时施加成型压力,保温10min后降温,冷却至室温后脱模,典型工艺曲线如图2所示。因为高温高压环境下树脂流动性强且本文采用单向带预浸料,有可能因为压力过大导致树脂挤出或纤维分散,因此通过在模压模具上模和下模中间加厚度,通过金属垫板来控制最终层合板的厚度,垫板厚度为理论单层厚度和铺层数的乘积。本文中考察不同冷却速率(–15℃/min、–8℃/min、–2℃/min)和成型压力(6.0MPa、2.0MPa、0.6MPa)对CF/PEKK复合材料成型质量和性能的影响,如表2所示。脱模后对制备复合材料进行机加和性能检测。
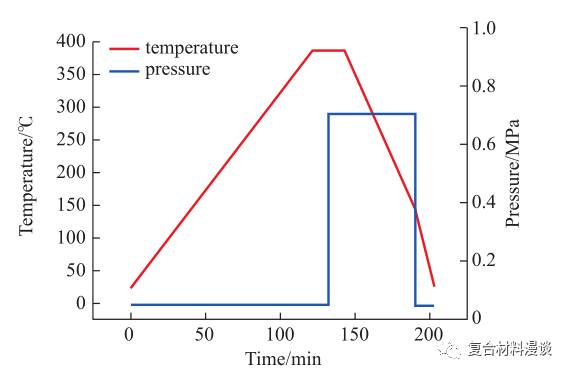
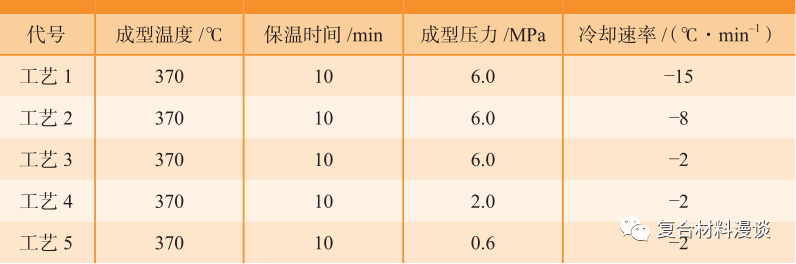
此外,为与CF/PEKK体系进行对比分析,本文采用自动铺丝结合模压成型两步法原位成型制备CF/PEEK复合材料层合板,本文采用的自动铺丝机与热压机如图3所示。首先以宽度6.35mm的CF/PEEK预浸料窄带为原材料,由法国coriolis自动铺丝机铺放CF/PEEK预制体,铺层与CF/PEKK一致,铺丝铺放过程采用激光加热铺丝头,加热功率设定为2200W,铺丝速度设置为0.06m/s,铺丝过程中压辊压力为800N。自动铺丝制备预制体后,将预制体移入模压模具采用模压后成型为最终层合板,模压工序与CF/PEKK体系一致,预热和成型温度设置为 370℃,成型压力 2.0MPa,冷却速率–2℃/min。
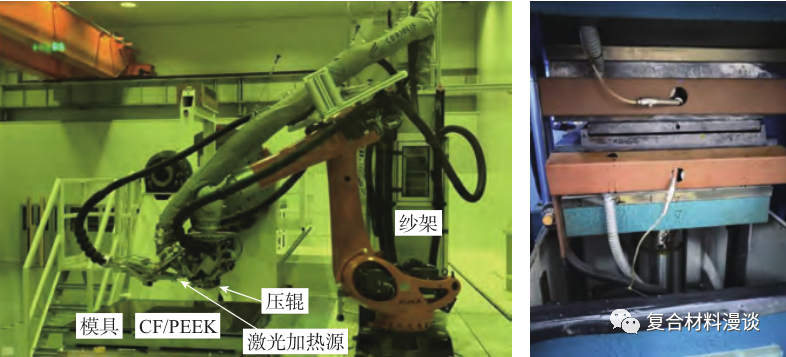
本文采用场发射扫描电镜(SEM)对预浸料微观形貌(图4(a)和(b))及复合材料破坏形貌进行观察;采用DSC测试预浸料的玻璃化转变温度、熔点;采用测厚仪测量层合板各区域厚度,利用超声波扫描显微镜采用超声水浸反射法(图4(c)),对层合板质量进行无损检测,检测范围为层合板全尺寸100%检测,探头5MHz,直径9.525mm,焦距20.066mm;参考ASTM D2344 Standard Test Methodfor Short-Beam Strength of PolymerMatrix Composite Materials and theirLaminates标准,采用 Instron 5965型5kN电子拉力试验机对试样进行短梁强度性能检测。试验过程中加载速度:1.0mm/min,采用三点式夹具,上压辊直径 6.00mm,下支辊直径3.00mm,跨距 8.00mm。测试温度为23℃,试验共测试有效试样6件;采用金相法依据GB3365《碳纤维增强塑料孔隙含量和纤维体积含量试验方法》,沿垂直于纤维轴向的横截面取样,长为20mm、宽为10mm、高为试验厚度,每组5个试样测试纤维体积分数和孔隙率,取平均值。
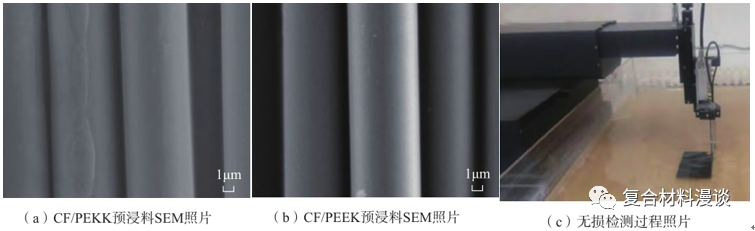
本文选用的两种碳纤维增强热塑性复合材料原材料同为聚醚酮树脂体系成熟单向预浸料带材。图5所示分别为CF/PEKK以及CF/PEEK预浸料照片,可以看出两种预浸料表面质量良好,纤维分散及树脂在面内分布均匀,结合图4两种预浸料的SEM照片所示微观形貌,也表明两种材料树脂包覆纤维表面,界面粘结良好,材料均匀性与一致性都较好。虽然同为单向预浸料带材,但是两种材料的规格形式有所差别,进而限制了其适用的成型工艺。图5(a)和(b)所示为Solvay公司推出的CF/PEKK预浸料,其幅宽为305mm,是面向手工铺放模压成型或热压罐成型开发的预浸料,本文选用高效低成本的模压成型工艺开展研究;对应地,TenCate公司的CF/PEEK体系同等幅宽(305mm)手工铺放预浸料研究开始较早,其模压成型研究已经比较充分。本文采用的是近年来专门适用自动铺丝工艺的6.35mm宽度的预浸料窄带,对其进行自动铺丝结合模压两步法非热压罐成型工艺研究。通过两种近年来新兴热塑性材料体系及适用工艺开展低成本非热压罐技术初步探索,为实际工程应用中材料体系选择提供一定的参考数据。
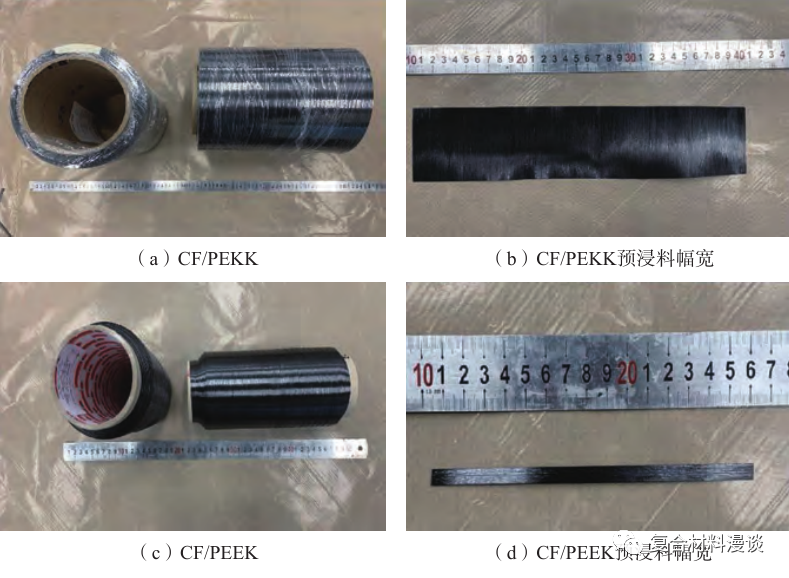
原材料理化性能,特别是树脂体系热机械性能是复合材料成型工艺窗口设置的重要依据,为了合理地设计与优化CF/PEKK热塑性复合材料体系的模压成型工艺制度,本文首先比较了CF/PEKK和CF/PEEK两种预浸料商品的Tg和Tm。其中,Solvay公司CF/PEKK预浸料的Tg和Tm分别为159℃和337℃;而TenCate公司的CF/PEEK预浸料Tg和Tm分别为143℃和343℃。为了验证商品手册数据可靠性,采用DSC对CF/PEKK预浸料Tg和Tm进行测试比对,测试条件为25℃到350℃两次升温,升温速率2℃/min,反应气氛和干燥气氛都是氮气,测试得到CF/PEKK体系的Tg为157.23℃,Tm为 337.20℃,与商品介绍信息接近。可以发现相比PEEK体系,PEKK体系的Tg稍高,而Tm降低6~7℃,说明PEKK 体系的耐温性不低于PEEK体系的情况下,有可能采用较低的成型温度,从而降低能耗,但是温度降低空间不大。
采用模压成型方法制备CF/PEKK热塑性复合材料层合板。本文研究中发现单层厚度控制是层合板质量的重要影响因素。图6所示为单层厚度控制优化前后制备的复合材料层合板照片及微观形貌。可以看出,工艺优化前层合板单层厚度控制较差,容易出现层合板翘曲和表面粗糙、不密实、均匀性差等问题(图6(a)),相应的其厚度方向微观形貌分析显示层合板层间存在明显的分层、孔隙等缺陷,如图6(b)箭头所示,大倍率SEM微观形貌(图6(c))显示纤维表面光滑,与树脂粘结差,显示弱界面特征;相反地,对单层厚度进行控制工艺优化后,制备的CF/PEKK层合板表面平整,光滑,均匀性好(图6(d)),微观形貌观察复合材料层合板层间无明显可视缺陷,各层层间粘结状态良好,显示典型的强界面粘接特征,如图6(e)(f)所示。
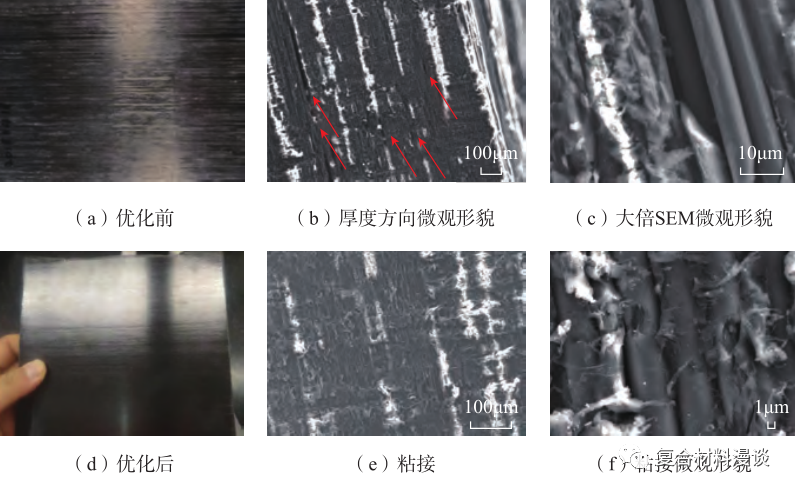
以短梁剪切性能为主要考察指标,进一步优化CF/PEKK体系模压成型工艺参数。短梁强度测试依据ASTM D2344进行,典型测试试样、过程照片及典型载荷–位移曲线如图7所示。可以看出,测试的6个试样应力–应变曲线重复性较好。值得注意的是,CF/PEKK热塑性复合材料体系在位移0.5mm附近载荷出现微小降低,之后随位移增大载荷恢复并继续增大,开始出现大变形,直到试样破坏,表现出明显的高韧性特性。
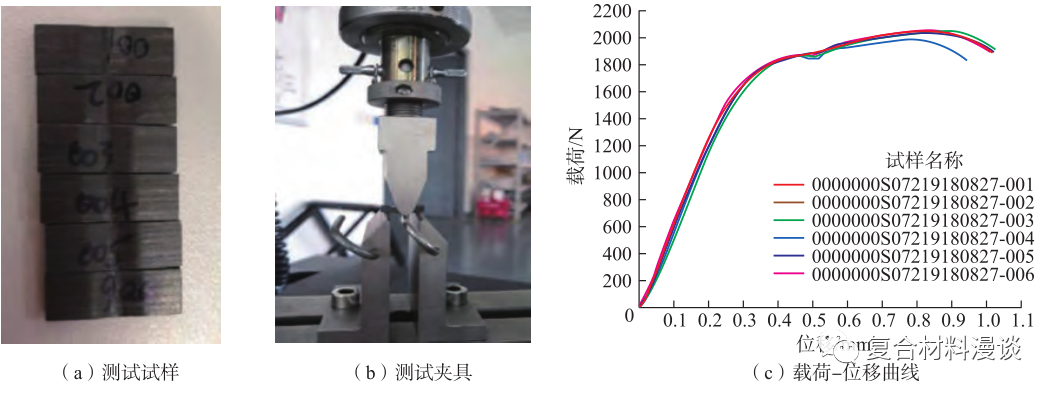
结合前文测得的材料Tg和Tm数据,参考材料供应商介绍及已有文献,模压成型温度设定为370℃,预热时间和成型时间设置为10min,本文主要考察成型压力和冷却速率对短梁强度的影响。按表2所述比较5种不同工艺的CF/PEKK复合材料层合板短梁强度,结果如图8所示。其中工艺1、工艺2和工艺3为相同成型压力和成型温度,冷却速率逐步降低条件下的短梁强度性能,可以看出,冷却速率对短梁强度性能有一定影响,但是影响不大,快速降温(–15℃/min)时短梁强度稍高,可能是由于快速冷却过程中大分子链段重排的松弛过程滞后于温度变化的速度,熔融状态中纤维/树脂良好的界面状态得以冻结甚至结晶,在一定程度上增强了复合材料层间性能;比较工艺3、4、5这3种工艺中成型压力对CF/PEKK短梁强度的影响,可以看出相同成型温度和冷却速率下,成型压力变化对短梁强度性能有一定影响,随着成型压力由6.0MPa(工艺3)降低到0.6MPa(工艺5),制备的层合板的短梁强度由118.95MPa先增大到135.65Mpa后再降低到129.73MPa,成型压力为2.0MPa时,制备的复合材料层合板短梁强度相比工艺优化前提高13.73%。这主要是因为成型压力促进树脂在层内以及层间的流动,影响树脂在纤维间的均匀分散。适当施加压力可以使高黏度的热塑性树脂在复合材料层间及层内分散更均匀,实现良好浸润从而提高材料的界面强度,同时使层压板更密实,减小空隙率,最终提高力学性能。但过大的成型压力会使树脂流动性加大,树脂在浸润流动迁移过程中还可能引起纤维的偏移或树脂溢出,反而导致力学性能降低。
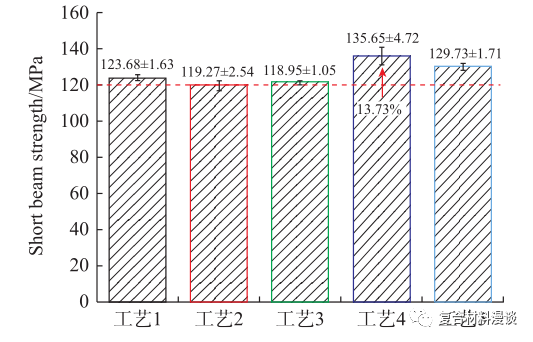
进一步对破坏后的短梁试样破坏断口进行分析,如图9所示,可以看出短梁试验过程中试样破坏为层间破坏模式,值得注意的是,高倍率下的SEM照片中CF/PEKK复合材料层合板短梁破坏断口表现出羽毛状破坏形貌,可能在破坏初期界面脱粘,但是高韧性树脂仍有粘接,随着应力不断增大树脂逐步延展至最终破坏,表现出高韧性破坏特性。
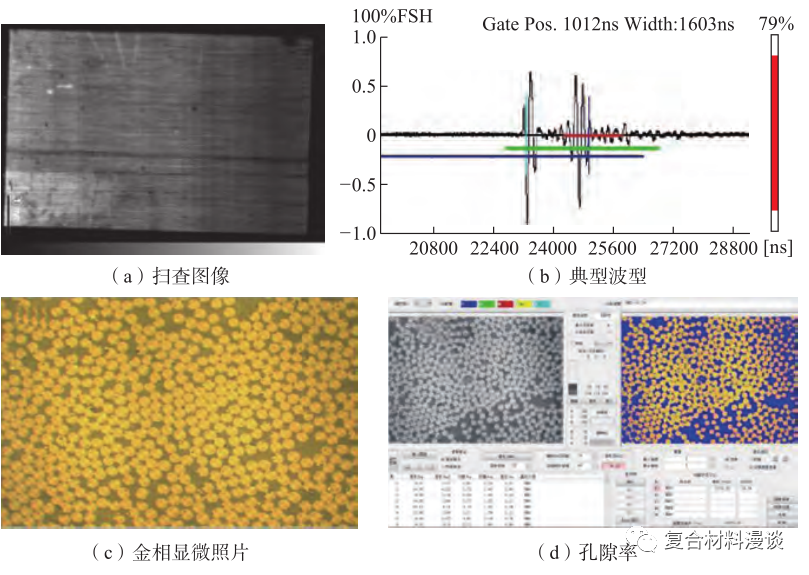
采用超声波扫描显微镜和金相检测对制备的复合材料层合板进行无损检测和纤维含量及孔隙率分析。得到工艺4对应CF/PEKK复合材料层合板的无损检测扫查图像及金相检测结果如图10所示。图10(a)和(b)分别为扫查图像和典型波形,可以看出,CF/PEKK层合板扫描图像亮度均匀,亮度高,检测波形界面明显,上表面和下表面界面清晰,波峰高,表明层合板内部结构致密,没有孔隙等缺陷,成型质量良好。图10(c)和(d)所示为典型金相显微照片、纤维含量和孔隙率,可以看出,制备的复合材料层合板纤维组织致密,测试5个试样取平均值,所得纤维体积分数为 61.8%,孔隙率为0。进一步表明成型质量良好,与短梁性能和SEM微观形貌特征一致。
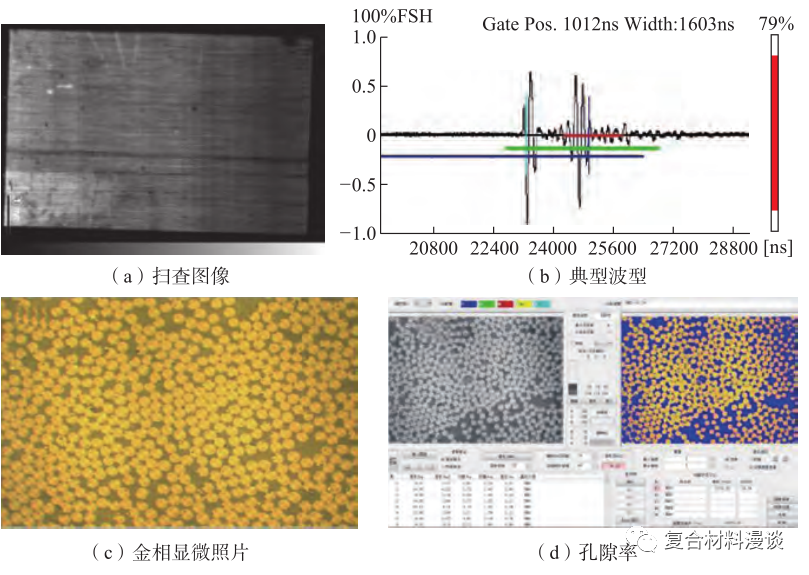
按前文所述热塑性复合材料层合板制备步骤,采用6.35mm宽度的 CF/PEEK 单向预浸料窄带,通过自动铺丝结合模压成型两步法制备CF/PEKK热塑性复合材料层合板。自动铺丝制备的CF/PEEK预制体及经过模压后成型后制备的 CF/PEEK层合板照片如图11所示。可以看出自动铺丝制备的预制体表面平整,但是可以看出CF/PEEK窄带间间隙,模压后成型后层合板更平整密实。采用磁力测厚仪测试层合板厚度计算单层厚度(CPT),测试得到的自动铺丝原位成型预制体的单层厚度为0.210mm,经模压后单层厚度降低至0.194m,这是因为自动铺丝过程铺丝压力较低,铺放过程中激光加热可以实现层间粘结,但是原位成型加热时间较短且压力较低,树脂在层间流动有限,因而自动铺丝预制体层间粘结较弱。经模压后成型后,模压过程中进一步施加压力,且加热加压时间充足树脂得以充分流动,层间间隙减小,单层厚度降低,层间粘结强度提高。
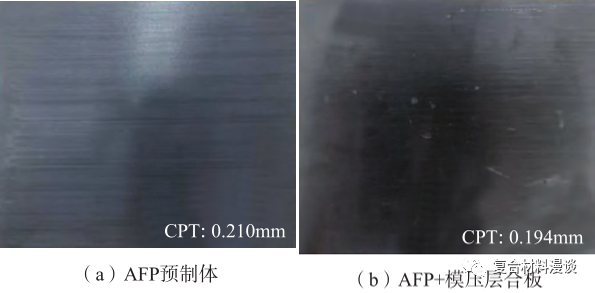
同样,对自动铺丝结合模压两步法制备的CF/PEEK层合板进行无损检测,并取样进行金相观察、短梁强度测试及破坏后试样SEM观察,如图12所示。可以看出同等模压工艺条件下(工艺3),与 CF/PEKK体系相似,CF/PEEK体系制备的层合板表面平整密实,金相观察没有明显大尺寸内部缺陷(图12(b)), 无损检测扫描图像(图12(a))显示大部分区域扫查图像亮度均匀,亮度高,表明层合板内部结构致密,成型质量较好。但是层合板边缘区域无损检测图像亮度有一定变化,主要是因为边缘少量树脂挤出导致。进一步参考 ASTM D2344测试标准进行短梁剪切试验,得到的载荷–位移曲线如图 12(c)所示,可以看出 6个试样重复性较好分散性较小,计算得到的短梁剪切强度平均值为(104.11±0.67)MPa,离散系数0.65%,稳定性较好。从图12(d)SEM所示破坏模式看,为层间剪切破坏和上表面压缩破坏的复合破坏,且出现多层层间破坏现象。
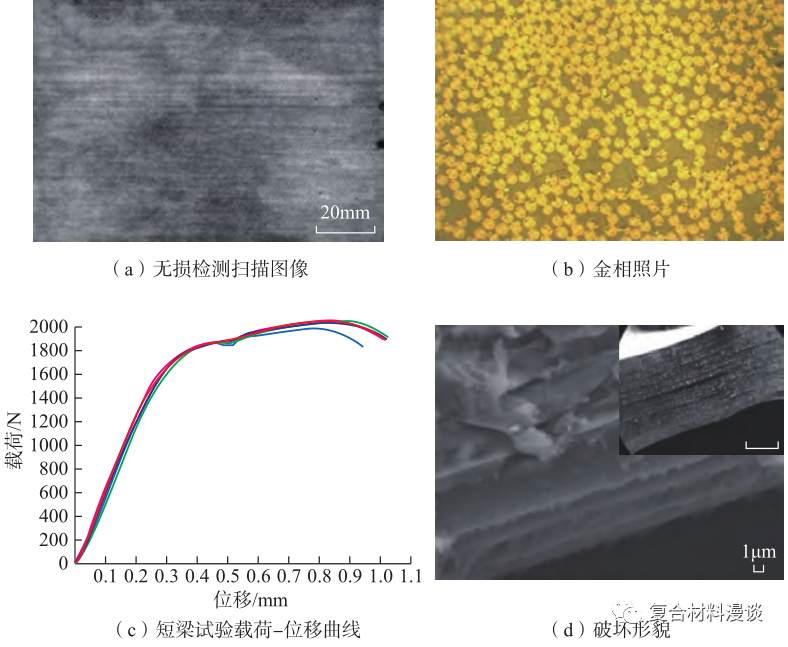
值得注意的是,虽然CF/PEEK复合材料与CF/PEKK体系短梁剪切破坏模式相近,都为典型的层间破坏,但是测试过程中自动铺丝CF/PEEK复合材料表现出与CF/PEKK体系不同的微观破坏行为。CF/PEEK 体系载荷–位移曲线显示载荷随位移增大而持续增大,直到最终破坏,没有在出现CF/PEKK体系(图 7(c))所示的载荷轻微下降后再回升现象。同时,SEM照片显示CF/PEEK 层合板破坏后断口比较整齐,没有出现与 CF/PEKK体系一致的羽毛状树脂裂纹(图9(b))。测试得到相同工艺条件下,CF/PEEK和CF/PEKK 体系的短梁强度分别为104.11MPa和118.95MPa,CF/PEKK体系稍高。这一方面是由于自动铺丝原位成型CF/PEEK预制体的过程中难免由于加热或铺放不均匀造成轻微的纤维损伤降低材料性能;另一方面,所对比的工艺条件成型温度为370℃,对于PEKK体系可能是较优的成型工艺温度,但是对于PEEK体系,因其熔点稍高,可能同等温度、压力和时间条件下树脂软化和流动不充分。关于CF/PEEK自动铺丝结合模压两步法成型工艺控制、两种体系表现出的破坏行为差异及相应机理有待进一步深入研究进行优化。
本文以备受关注的CF/PEEK和CF/PEKK热塑性预浸料体系为研究对象,对其适用的低成本模压成型、自动铺丝结合模压两步法原位成型两种工艺进行初步探索,并对两种体系的材料及性能进行对比分析,研究结果可为未来航空主承力结构热塑性复合材料的材料体系选择提供数据基础和参考。主要结论如下:
(1)对比分析了所选用CF/PEKK和CF/PEEK单向带预浸料的表面状态、微观形貌、规格形式及Tg、Tm,分析了材料质量特点及工艺适用性差异。建议 305mm幅宽CF/PEKK 体系采用模压成型,而6.35mm宽CF/PEEK窄带采用自动铺丝结合模压两步法成型工艺。
(2)对CF/PEKK复合材料模压成型工艺进行了初步优化,发现控制固化后单层厚度是成型良好的关键。比较不同成型压力和冷却速率下CF/PEKK层合板短梁强度,发现冷却速率对短梁强度影响不大,成型压力对短梁剪切强度有一定影响。在成型压力2.0MPa、成型温度370℃、冷却速率–15℃/min工艺条件下,CF/PEKK复合材料短梁强度达到(135.65±4.72)MPa,破坏断口微观形貌表现出明显的高韧性特征,无损检测及显微观察证明得到复合材料成型质量良好,对应纤维体积分数为61.8%,孔隙率为0。
(3)初步探索了CF/PEEK体系自动铺丝结合模压两步法原位成型工艺,与 CF/PEKK同等工艺条件下(成型压力2.0MPa、成型温度370℃、冷却速率–2℃/min)成型质量良好,破坏模式相近,但是短梁强度较低,微观破坏行为有一定差异。说明虽然同为聚醚酮体系,但是CF/PEKK和CF/PEEK体系在具体成型工艺和性能上仍有差异,建议进一步研究优化,本文结果可为后续研究提供数据参考。
2021, 64(11): 50–57, 68.
原文始发于微信公众号(复合材料漫谈):模压成型 CF/PEKK 与自动铺丝 CF/PEEK 热塑性复合材料对比研究