
热塑性复合地梁的AFP制造
复合地梁并不新鲜,但使用热塑性预浸料带和先进的纤维定向技术进行制造却是新的,而GKN Fokker和Mikrosam在开发和制造用于多功能机身展示器(MFFD)下半部乘客舱地网的12个TPC梁时已经成功地进行了演示。
所有图像的照片来源:GKN Fokker,Clean Sky 2/Clean Aviatio
导 语
“Multifunctional Fuselage Demonstrator(MFFD)”为下一代机身铺平了道路,该机身使用热塑性复合材料(TPC)而不是主要由热固性复合材料(大多数为碳纤维增强环氧树脂)制成,这是目前用于航空结构的材料。”
由欧盟联合研究和创新计划“Clean Aviation”资助,MFFD正在推进的材料和工艺将使飞机生产量增加,例如每月生产70-100架窄体飞机。这些技术还将通过使用重量更轻的复合材料以及通过将大部分紧固件替换为TPC焊接以生产用于最终装配的集成结构模块来降低成本和减少二氧化碳排放。该项目最终的8×4米机身部分将于2024年初完成,这将是有史以来建造的最大的全TPC结构。
GKN Fokker(荷兰霍赫芬)领导了MFFD下半部分的生产,该项目属于STUNNING子项目。下半部分于2022年末完成,并被运往德国斯塔德的Fraunhofer IFAM,后续将使用与德累斯顿的Fraunhofer IWS合作开发的先进激光原位连接工艺与上半部分连接。下半部分包括用于货舱地板的结构网格和用于客舱地板的另一个网格。后者由12个TPC地梁组成,带有焊接的TPC支架用于连接金属座椅轨道,以及焊接的TPC垂直支撑杆用于将地网连接到机身框架上(如图1所示)。
本文讨论了GKN Fokker与设备供应商Mikrosam(马其顿普里莱普)合作,开发TPC地梁的两年过程,包括使用拖曳转向的创新自动纤维铺放(AFP)层压策略,随后进行热压固化。后续开发采用特别设计的压力机和气囊概念,在没有热压釜的情况下实现固化,以生产未来用于TPC方向舵的6米长桁条。

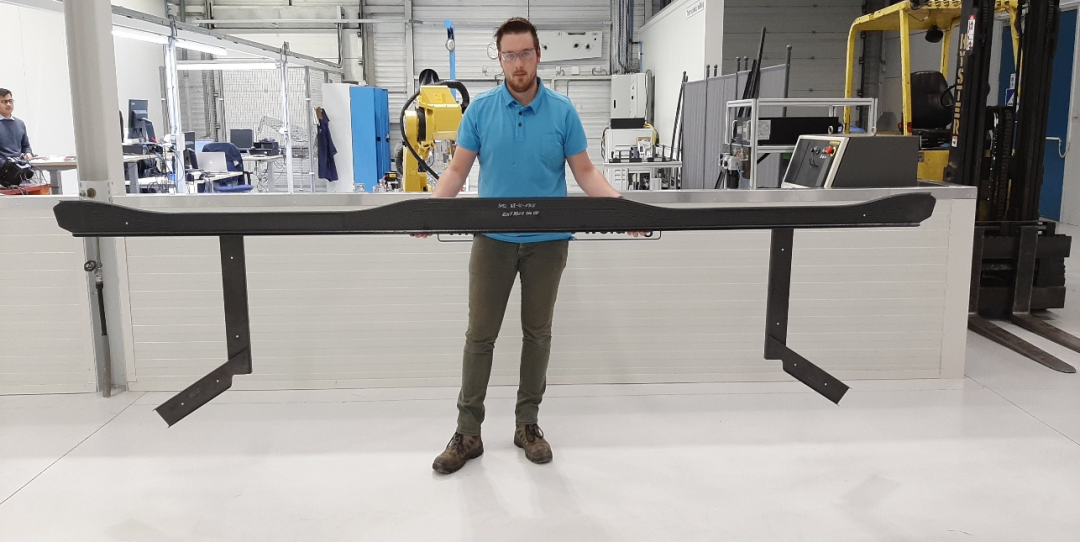
图1.用于客舱地网的全尺寸梁。
MFFD下半部分顶部包括用于客舱地板的结构网格,包括金属座椅轨道(上图)。GKN Fokker生产了12个CF/LM-PAEK地梁,带有传导焊接的垂直支撑杆(下图),然后将在成品模块中传导焊接到机身框架上。
01 AFP层压和工具
MFFD地梁具有C型截面,在其长度上具有不同的腹板高度和厚度。GKN Aerospace(英国索利赫尔)全球技术中心荷兰(GTC-NL,霍赫芬)主任Arnt Offringa表示:“形状与波音787地梁非常相似。梁上通常会有凹槽,以便为电气和其他系统留出空间。几何形状和层压的复杂性是我们选择AFP的原因,开发的过程是GKN Fokker和Mikrosam的共同努力。”
GKN Fokker开发了一种策略,将两个梁预制件同时放置在一个带有切割通道的成型钢芯上。后者有助于在固化之前将层压剪成两个预制件(图2)。同时,这种高效方法,比分别制作预制件的废料要少得多。
图2 GKN Fokker 开发了一种带有中间切割通道的成型钢芯, 以便将单个AFP层切割成两个MFFD地梁预制件。
Mikrosam公司总经理Vele Samak认同这种方法,并表示:“这种方法通过优化AFP路径,最大限度地减少了叠层时间。在转动芯轴的同时不断铺设纤维,最小化了切割和重新启动的次数。这有助于保持一致的质量并简化了整个工艺流程。它还保持了纤维的良好张力,有助于防止翘曲并实现几乎固化的叠层。这有助于缩短后续固化步骤的循环时间。” “为了加快开发进程,”Offringa表示,“首批梁件是在Mikrosam的研发中心生产的。” 随后的梁件则是在GTC-NL安装的Mikrosam全新8轴AFP机器上制造的。该中心还安装了Mikrosam的设备,用于分条热塑性预浸料带和定制的压实机,稍后将讨论这些设备。” Vele Samak提到:“AFP机器具有模块化的多材料头和高温激光加热系统。GKN Fokker目前正在使用它来开发热塑性技术,但未来他们也可以用于干纤维或使用热塑性粘合剂的热塑性预浸料带。我们的AFP头是模块化的,因此可以将相同的头附加到不同的配置上,而无需进行修改。因此,随着新技术的发展,它提供了很多灵活性和可升级性。” Offringa指出,开发始于来自Solvay Composite Materials(美国佐治亚州阿尔法雷塔)的材料。但是,STUNNING地板梁是使用Toray Advanced Composites(荷兰尼耳威达尔)的Cetex TC1225带材制成的,其包含T700碳纤维(CF)和低熔点聚芳醚酮(LM-PAEK)基体。该材料系统被选择用于STUNNING示范项目的整个过程中,并由MFFD项目领导者空客输入。虽然Mikrosam的AFP喷头可以同时放置四条带材(1英寸宽),但决定在铺装过程中使用两条带材以适应几何形状,并在地板梁的低半径边缘实现更好的熔合。
02 纤维转向,优化设计和工艺 Offringa表示:“使用纤维定向的叠层策略在制造开发过程中逐渐发展。”“在AFP出现之前,我们总是坚持使用0°,90°和45°的叠层。但是使用AFP,我们需要并希望使用纤维定向来实现双曲面板而无褶皱或间隙,并且使纤维最佳定向以承受结构负载。纤维定向在制造中相对较新。但我们将会越来越多地在AFP中看到它,从而从传统的标准叠层中偏离越来越多。” 在梁的铺放过程中,首先放置了一个径向的第一层,这与通常的90度角略有偏差,Samak解释道,“这样可以实现纤维的连续性,并良好地固定在芯轴上。由于这层下面没有东西可以与之融合,使用了较低的温度。为了更好地固定在钢芯轴上,使用了Kapton [高温聚酰亚胺]胶带。”
03 零度层 Offringa解释说,“0°方向沿着梁”,“在最终叠层序列中,0°铺层不再停留在半径区域,而是停留在网的较平坦区域的斜坡下方[图3示意图]。该图示出了这两种策略。左侧的梁是使用非优化的叠层制造的,而右侧的叠层真的非常优美。它减少了间隙和重叠,并改善了叠层过程。” 需要注意的是,图3中显示的叠层是在弯曲的芯棒上建立的。Offringa继续解释道:“在左侧的图像中,纤维要么在整个梁的长度上连续,要么在梁的这个倾斜部分开始和停止,这并不容易。你试图创建梁的这个弯曲部分,但是通过停止每个0°的叠层,你创造了一个拐角。由于梁的复杂形状,也不容易在这些位置开始和停止。因此,Mikrosam的工程师帮助我们修改了AFP叠层程序,以使纤维更易于控制,以获得相同的性能,但采用更友好的制造工艺。” 图3. GKN Fokker与Mikrosam合作优化地板梁 自动纤维排列(AFP)铺放工艺。 左侧的铺放工艺未被优化,而右侧的铺放工艺中,0°角的纤维层不再停留在半径区域内,而是在较平坦的区域进一步向下斜坡铺放。这减少了纤维层在难以处理的区域开始和停止的情况,以及缺口和重叠,使AFP工艺更加高效。
04 优化工艺参数和45°层 MikroPlace软件被用于生成AFP叠层过程的机器代码。首先,设计好的叠层、纱线落点、间隙/重叠和可能的碰撞问题在MikroPlace中进行了模拟,然后与GKN Fokker团队一起分析解决方案,例如第一层的更大角度以及不同的叠层花瓣策略。 MikroAutomate软件随后被用于模拟在线机器控制。Mikrosam,高级复合材料和机器人研究所(IACR, Prilep, Macedonia)和GKN Fokker团队优化了关于工艺参数的铺层设计。“例如,”Samak解释说,“改变AFP头的角度以避免碰撞将改变激光角度,从而导致不同的加热区域。可能需要修改铺层温度来解决这个问题。” 他继续说道:“我们的AFP机器控制软件允许您微调在课程和层的不同部分中的激光输出量。使用标准控制,只按照AFP头的速度输出功率是不够的,例如,在陡峭的曲线处。可能需要在这个特定的部分减少一些激光输出,以避免烧毁进入的材料。” 在地梁的另一个优化是在45度角的铺层上。Samak指出,MikroPlace软件可以为每个带子的每个角度铺层单独指定规范。“这意味着我们的软件允许更细微地修改每个铺层的带子路径,”他解释道。“当您为45度的铺层编程AFP头时,您最终会在梁的中间臃肿区域产生带子偏差,其中您会上升然后再下降。因此,当您进行45度的铺层时,您必须手动解决发生的偏差。MikroPlace软件允许团队微调这些铺层,以便没有间隙或重叠。” 关于相邻叠层的检测,Offringa解释说:“我们的AFP机器上没有在线检测系统。但是我们使用了一个过程摄像头和一个热成像摄像头来记录叠层过程。通过这两个摄像头,操作员可以监控叠层过程中是否存在任何间隙或重叠,并且还可以看到它们是否超出了预期目标。例如,如果进料带更薄,那么它会在热成像摄像头上立刻被发现,因为该区域将被加热得不同。如果必要,操作员可以停止叠层并解决这个问题。”
05 热压固化,地板网格组装 在完成每个叠层后,将其切割成两个预制件。然后,所有12个预制件均在高压釜中压实成TPC梁,以最小化成品结构中的孔隙率。Offringa表示:“我们使用标准的高温Kapton热塑性薄膜真空包装预制件,并在6小时的高压釜循环中施加6bar的压力。唯一需要的整理工作是将翼缘切割到所需宽度。” 将梁焊接到已经安装了框架的下部机身外壳中,这些梁可以组装成MFFD地板网格。地板梁与机身框架之间的连接是通过最新的传导焊接工艺实现的,该工艺使用带有铁砧的加热棒元件施加反向压力。使用一个被加热和冷却的元件,通过接触被连接的零件来传导。该元件安装在机器人上,机器人将其移动到每个焊接位置。在SAM|XL,这个机器人安装在一个龙门架上。”SAM|XL是荷兰代尔夫特理工大学(TU Delft)校园内的智能先进制造XL研究中心,MFFD下半部分装配是在该中心完成的(图4)。 图4. 由 GKN Fokker 领导的 STUNNING 项目已经完成了 MFFD 下半部的组装,如 SAM | XL 所示。 该模块已经被运送到德国施塔德的夫琅和费 IFAM,在那里它将使用由夫琅和费 IWS (德国德累斯顿)开发的基于激光的焊接工艺连接到上半部分。图片来源: SAM | XL
根据Offringa的说法,“开发这些梁是整个STUNNING项目的一部分。我们于2021年初开始,并花费了大约9个月的时间。当然,我们必须安装设备,并且Mikrosam帮助我们解决了问题——在我们的新AFP机器投入运营之前,他们制造了前两根试验梁。然后,我们将模具转移到GTC-NL,并继续进行开发。我们用了大约6个月的时间为MFFD制造了12根梁。”
06 OOA固化工艺 与此同时,GKN Fokker还开发了一种新颖的无热压罐(OOA)固化工艺,可用于生产长达6米的梁和桁条。“我们目前制造这种尺寸的TPC桁条时,希望能够不使用热压罐进行生产,”Offringa解释道。“OOA固化不仅减少了周期时间,还减少了需要的能源和辅助材料。我们之前已经将这种技术用于机翼肋骨的生产,但是希望将其扩展到更大的零部件上。” 为此,GKN Fokker开发了具有集成压力、加热和冷却系统的体系,并在由Mikrosam建造的专门设计的固化压机中使用了这个系统。 图5. GKN Fokker 采用OOA工艺进行固化。 这套系统具有集成的加热和冷却功能,并使用气囊 (以红色显示) 施加压力。
07 集成工具 “你经常会看到这些集成工具用于树脂传递成型(RTM)中,”Offringa说道。RTM是一种模压工艺,传统上采用液体树脂(通常是环氧树脂)注入干燥纤维毡,在RTM模压机中施加压力和热固化。GKN Fokker并未使用液态或热固性树脂,但却使用这些集成工具来施加温度和压力以固化TPC毡坯。值得注意的是,GKN Fokker制造的TPC零部件可能与RTM竞争,以在复合材料航空结构中实现更高的生产率。 Offringa解释说,在GKN Fokker OOA压实工具中,“使用水进行冷却,而传统系统或感应可以用于加热与TPC预制件接触的工具表面。冷却比加热更重要。如果冷却不在零件表面的整个面积内均匀,那么就会先在一侧缩小,然后在另一侧缩小,这将导致零件缺陷。”虽然感应加热对于高温加热来说实际上是即时的且非常节能,但这些系统在冷却期间会有什么挑战吗?Offringa表示:“感应加热确实非常快速,冷却有点棘手,必须与工具设计相结合进行控制。”
08 新型压力机和气囊 GKN Fokker’s OOA系统被放置在由Mikrosam提供的新型压力机内。Samak表示:“这是我们建造的第一台定制压力机。压力机通常不是我们的核心业务,但我们有良好的工程能力,GKN团队看到我们可以与他们合作建造非常定制化的压力机,在其中他们可以集成自己的加热和冷却机制。” Offringa说:“这台压力机就像一个6米长的钢盒子,在这个盒子里,您可以放置带有自己的加热,冷却和加压机制的工具。这是一个模块化系统,用于制造各种零件。对于加压,我们使用的是一个气囊系统。” GKN Fokker 的工艺与传统的热固性树脂浸渍成型(RTM)有所不同。Offringa解释说:“我们的压机是一个简单的概念,基本上类似于锁住门。它不是一个巨大的气动或液压压机,而更接近于Coexpair(比利时纳慕尔)使用Radius Engineering(美国犹他州盐湖城)许可证制造的RTM压机。”请注意,Coexpair为Spirit AeroSystems在苏格兰普雷斯特威克(Prestwick)为空中客车A320制造的复合材料扰流板提供RTM压机。Offringa补充说:“Coexpair最近提供了一台12米的RTM压机,与Mikrosam为我们建造的那台有些相似,但使用了不同的开合系统。它们非常具有成本效益。” Offringa继续说道:“因此,我们的压力机非常简单,气囊也非常简单。它不是金属,而更像消防水带,具有柔韧性和耐压性。你将预成型件与气囊系统放入模具中,在顶部进行简单的操作,就能施加10-15bar的压力到整个预成型件上。在这个压力机中,我们几乎没有任何运动,但是从顶部和两侧施加压力。” Samak指出:“这个系统也是模块化的,这为未来的生产提供了很大的灵活性。” 图6. OOA工艺链用于未来TPC。 在另一个LIFT项目中,GKN Fokker使用上述工艺链为展示型倾转旋翼飞机的V型尾部生产了一根TPC梁。采用自动铺带(ATL)系统和集成超声波接合机生产平板定制毛坯。然后使用简单的预成型压机将这些毛坯预成型成C形,并将其放入Mikrosam固化压机中生产最终零件。
09 未来TPC结构的生产 因此,MFFD地板梁项目不仅推动了大型焊接热塑复合材料机身模块的发展,还为GKN Fokker更高效地生产更大型的热塑复合材料航空结构奠定了基础(见图5)。Offringa表示:“我们在荷兰的工厂里生产商务飞机的方向舵和升降舵。升降舵长度为6米,之前一直采用真空袋和热压固化工艺制造桁条,现在我们将其转为OOA,消除了真空袋制造所需的人力和材料,同时将周期时间缩短了80%。” 这种更具可持续性的TPC结构的生产在第二个清洁航空项目LIFT中得到了进一步发展,在该项目中GKN Fokker与Leonardo直升机公司(意大利Samarate的Cascina Costa)合作为一款飞行倾转旋翼飞行器生产了一个TPC尾结构。Offringa说:“这个尾翼结构也是使用AFP制造的,具有简单的C形结构成员。我们使用了一个工艺流程在GTC-NL中安装。我们首先使用一个自动覆盖带机器制作了一个平坦的毛坯,该机器使用超声波固定系统将覆盖层粘合在一起。然后我们使用一个简单的伺服控制成形压机。覆盖带机器和成形压机来自Boikon [荷兰Leek]。最后,我们将毛坯放入Mikrosam的压实机中,产生最终的TPC零件。”那么,GKN Fokker的下一步是什么?Offringa说:“将OOA成形和共同固化技术扩展到更具挑战性的应用,如复杂的桁架和梁以及整体加强的外壳。”
信息来源: https://www.compositesworld.com/articles/mffd-thermoplastic-floor-beams-ooa-consolidation-for-next-gen-tpc-aerostructures-
免责声明 | 本公众号尊重版权并感谢每一位作者的辛苦付出与创作,部分素材源自网络,版权归原作者所有;如涉版权问题,请第一时间联系我们。
【end】 关注我们,获取行业最新动态
编译:温棠 美编:吉晨睿
东华经纬新材料研究院 立足国内顶尖观察 链接全球最新行业动态 点亮“在看”与“星标” 与我们携手共奋进!
原文始发于微信公众号(东华经纬新材料研究院):GNK开发热塑性层压板非热压罐固化工艺降低制造成本
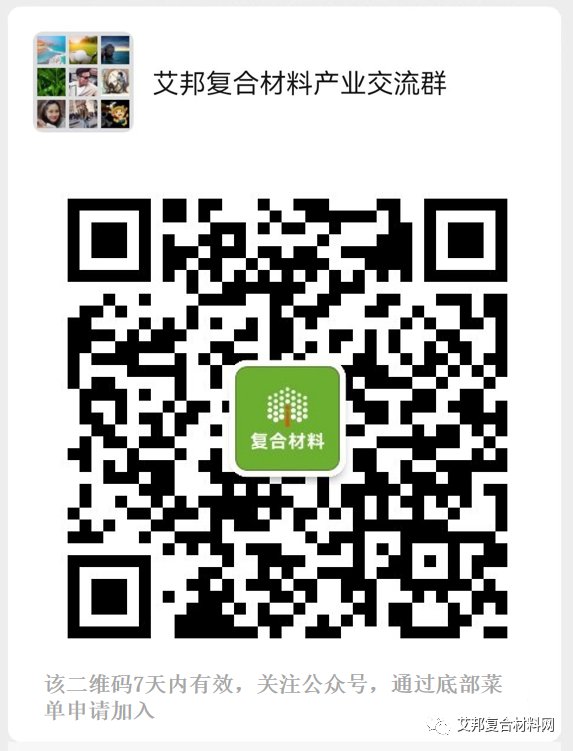