摘要:为了解决电动汽车的续航和强度刚度问题,以某汽车的电池箱为研究对象,实际测量尺寸并在 CATIA 中建模后导入ABAQUS建立仿真模型,进行电池箱的2种组合工况下的静强度和约束模态分析。针对电池箱的仿真分析结果,再使用碳纤维复合材料 T300/5222 进行材料替代,运用等代设计法对 T300/5222 的厚度进行设计以及铺层角度确定,结果表明,复合材料电池箱的动静态性能提高,电池箱质量降低,轻量化效果显著。
随着国家科技的发展以及人们生活水平的进步,电动汽车逐步进入人们的视野并且逐步占据汽车市场的较大份额[1],同时电动汽车的一系列问题也慢慢浮现出来。首先电池质量占整车质量的 20%~30%, 而箱体质量占电池包总质量的10%~20%[2];其次电池箱目前大多数都使用的是金属材料,虽然金属有着在抗冲击性能和导热性方面很大优势,但是它很大的缺点就是质量太大[3]。本文采用碳纤维复合材料对原金属电池箱进行设计,由于碳纤维复合材料本身具有比刚度、比强度高,密度小的优势 [4],所以可以很好地解决金属电池箱质量太大的问题。
1.1组合工况静强度和静刚度分析
为了更好地模拟汽车行驶过程中电池箱的运 动情况,采用 2 种组合工况对电池箱进行仿真分析计算,组合工况 1 为颠簸路面急刹车工况,组合工 况 2 为颠簸路面急转弯工况 [5]。这里金属电池箱采 用的材料是 Q235, 其弹性模量为 210 GPa,密度为 7 850 kg/m3, 泊松比为 0.3, 屈服强度为 235 MPa, 电池箱仿真边界条件为固定电池箱底部 12 个螺栓 孔的 6 个自由度。
电池箱急刹车、急转弯工况加载方式见表 1。图 1 为颠簸路面急刹车工况的仿真云图, 由图 1(a) 可知,该工况下最大变形量为 0.252 mm;由图 1(b) 可知,该工况下最大等效应力为 54.46 GPa。
图 2 为颠簸路面急转弯工况的仿真云图, 由图 2(a)可知,该工况下的最大变形量为 0.22 mm;由图 2(b)可知,该工况下的最大等效应力为 51.2 GPa。
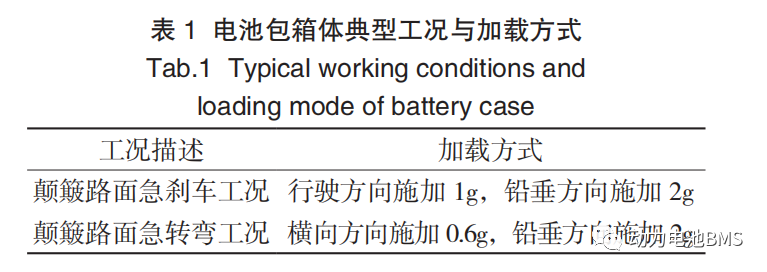
1.2 模态分析
模态分析是通过仿真软件求解得到物体的模 态相应参数,以此来判断物体结构设计的合理性, 也为后续的设计和优化提供数据支撑。振动方程表达式为[M]{q}+[K]{q}=0 (1)
式中:[M] ——质量矩阵;[K] ——刚度矩阵;{q} —— 加速度;{q } ——速度。当某物体在振动过程中做简谐运动,位移可 以表示为{q (t )}={q0}sin( ω t+ ψ ) (2)
式中:{q (t )}——时间的位移向量;{q0}—— 固有振 型;ω ——固有频率;ψ ——相位角。
将式(2)代入式(1)可得:([K]-ω 2[M]){q0 }=0 (3)
在物体振动过程中的 {q0} 不可能全为 0,则物 体的固有频率函数式为│[K]-ω 2[M] │=0 (4)约束模态比自由模态更能体现出电池箱的动 力学特性,所以对电池箱进行完全固定约束,求解 前 2 阶电池箱的约束模态如图 3 所示。1 阶约束模 态为 28.3 Hz,2 阶约束模态为 29.6 Hz。
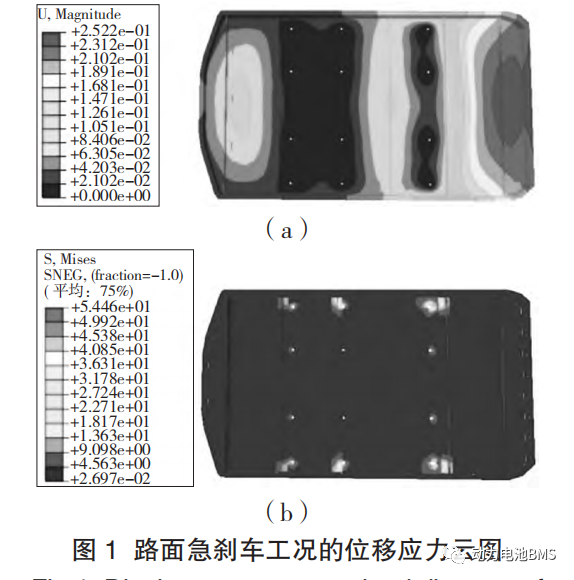
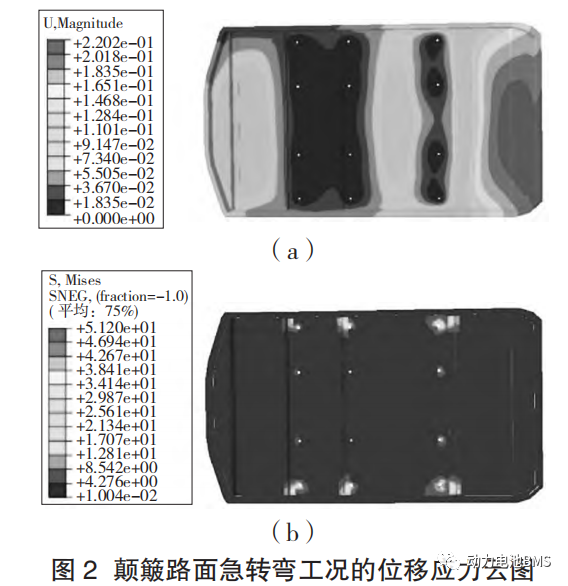
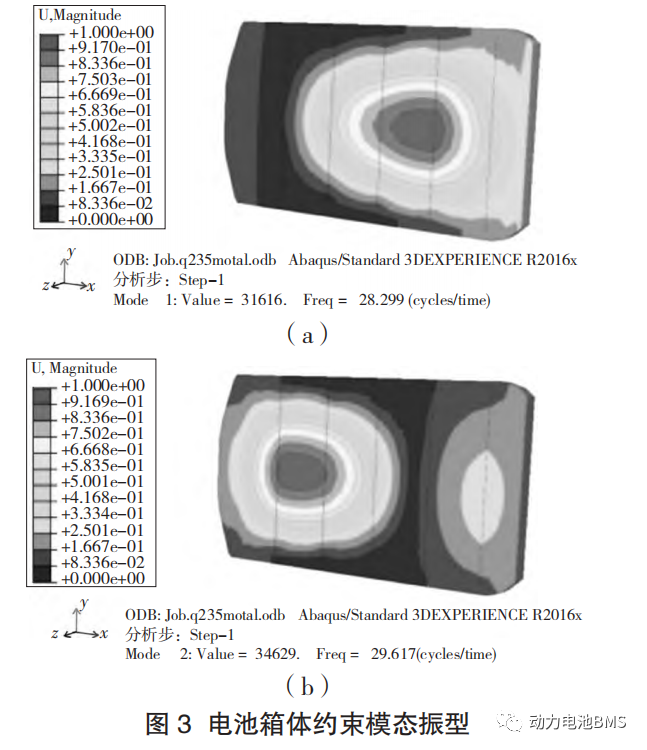
本文将对某车电池箱采用碳纤维 / 环氧 (T300/5222) 复合材料代替原 Q235 材料。公众号动力电池BMS,碳纤维 复合材料比强度与比刚度都比普通金属材料高, 而且质量很轻 , 是进行轻量化研究较好的材料选 择。在 ABAQUS 中模拟碳纤维复合材料材料模型, T300/5222 具体材料参数如表 2 所示。
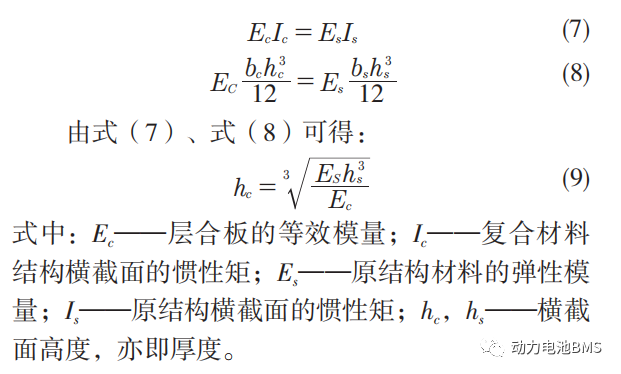
碳纤维复合材料不同的铺层有着不同的性能。铺层的准则有:对称铺层原则、顺序原则、定向原则、 按承载选取原则、最小比例原则等。合适的铺层 形式往往可以使得电池箱有着足够的强度和刚度。碳纤维复合材料中的 90°铺层可以承受横向载荷 , 0°铺层和 45°铺层分别可以承受轴向载荷和承受 剪切载荷 [6]。进行铺层设计时也需考虑各铺层角度 所占的比例和铺层位置对电池箱的影响。现有研究 结果表明,当碳纤维复合材料的铺层角度为 [45/- 45/90/0]ns 时,文中所关注的碰撞性能在几种角度 中是最好的。因此本文将初步设置碳纤维复合材料 防撞梁的铺层角度为 [45/-45/90/0]ns。当铺层角度 确定后,需使用等代设计法对所替换材料的厚度重 新计算 , 以满足相应的设计需求。
假设电池箱的载荷类型是弯曲载荷,平板尺 寸为 b×l×h,其受到的最大弯曲载荷为 M,如图4 所示。
板件的最大挠度公式可以根据材料力学中的 平板弯曲理论得出:
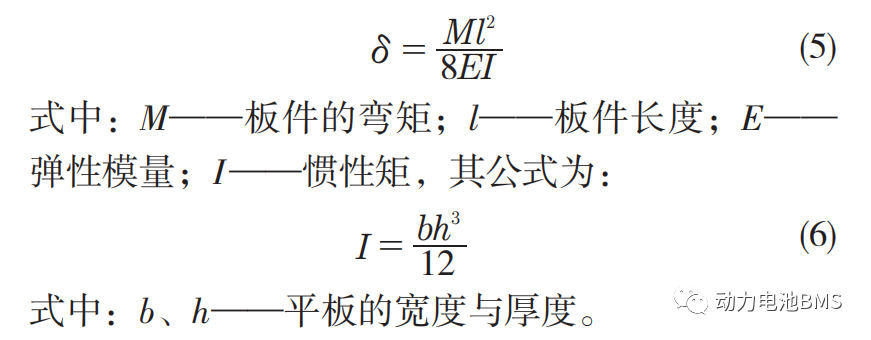
为了保持电池箱的安装精度不变,同时不对 电池箱附近的其他结构产生影响,本文将碳纤维复 合材料防撞梁的铺层角度初步设置为 [45/-45/90/0] 4s,采取对称铺层,这种铺层角度是准各向同性的 角度,整个平面内的模量在各个方向相等,因此采 用这种铺层角度的碳纤维复合材料电池箱可以采用 等效模量进行抗弯刚度计算。
通过等刚度近似理论进行设计, 最终 2 种材料 的抗弯刚度应相等:
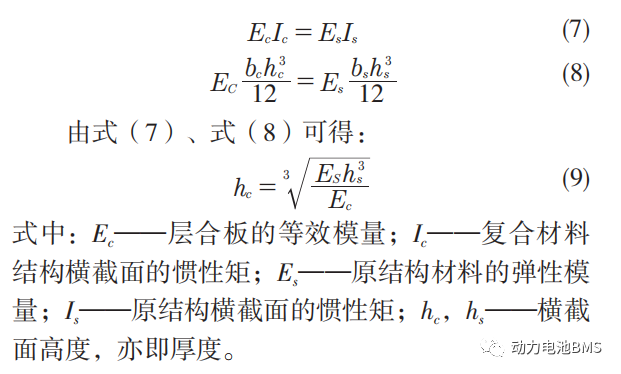
据此可初步计算出等刚度替换后新材料的厚 度,但是为确保替换材料后结构的刚度满足要求 , 通常会根据不同板件的位置对其厚度进行调整。根 据文献可知,板件刚度是厚度的非线性函数,近似表达式为 :
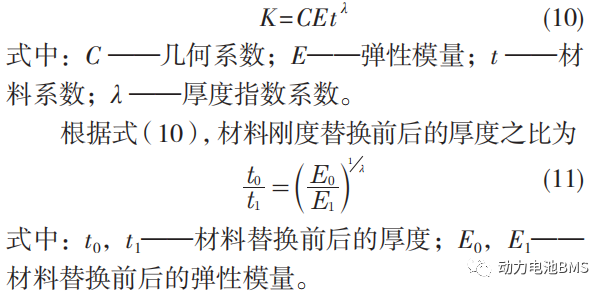
对于汽车车身部件 , 取值通常为 1~2,本文 λ 取值为 1.2。
图 5 为复合材料电池箱颠簸路面急刹车工况的 仿真云图,具体的加载方式和金属电池箱相同。
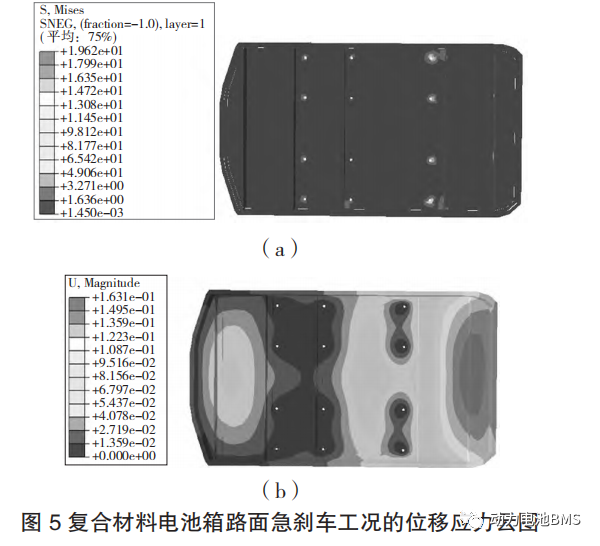
由图 5(a)可知,颠簸路面急刹车工况下的 最大应力为 19.62 GPa;由图 5(b) 可知, 颠簸路 面急刹车工况下的最大变形量为 0.163 mm。
图 6 为复合材料电池箱颠簸路面急转弯工况的 仿真云图,具体的加载方式和金属电池箱相同。由 图 6(a)可知,颠簸路面急刹车工况下的最大应 力为 15.7 GPa。由图 6(b) 可知, 颠簸路面急刹 车工况下的最大变形量为 0.128 mm。
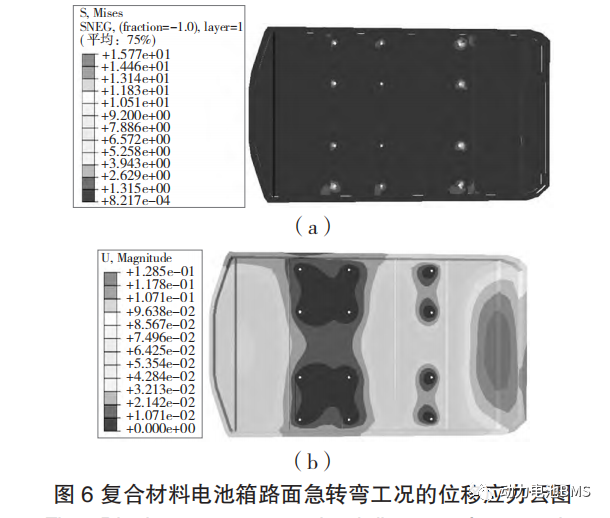
由图 7 可以看出,使用碳纤维环氧复合材料 HT3/5222 替换后的电池箱,1 阶约束模态 44 Hz,2 阶约束模态为 52 Hz。2 种材料的电池箱的性能情况见表 3。
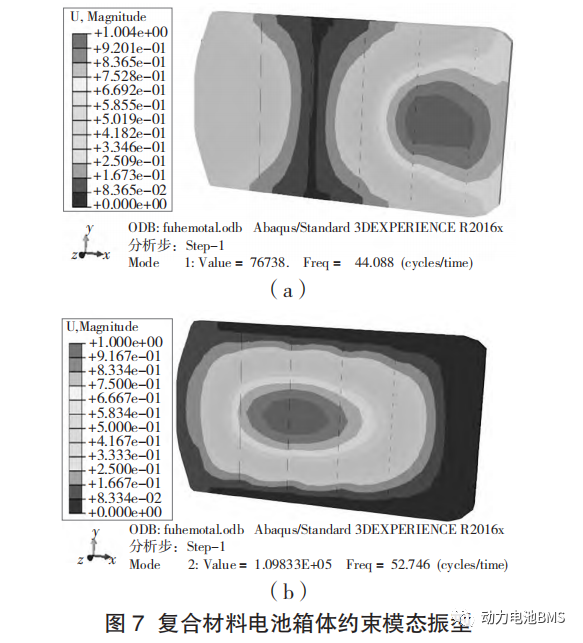
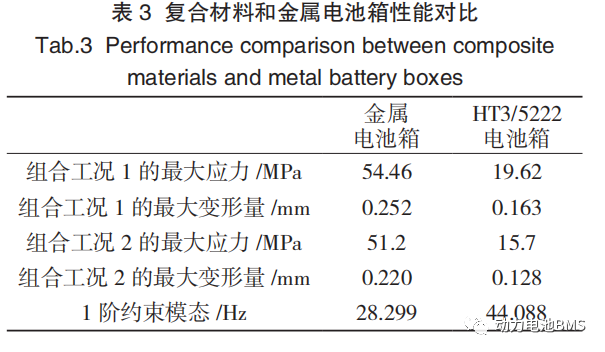
本文以某汽车的电池箱为研究对象,对其进 行 2 种组合工况的静刚度分析和约束模态分析。然 后使用等代设计法,使用碳纤维环氧复合材料对原 电池箱金属材料进行替代。
数据显示,复合材料电池箱在组合工况 1 的 最大应力相对于金属电池箱降低了约 25 MPa,降 低了 50% 以上,最大变形量降低了 0.097 mm;组合 工况 2 最大应力相对于原电池箱降低了 25.7 MPa, 最大变形量降低了 0.102 mm。1 阶约束模态提高了 16 Hz。结果表明,经过复合材料替代后,电池箱动静态性能得到提高,减重效果优异, 轻量化效果 显著。
注:文中观点仅供分享交流,转载文章的版权归原作者所有,如涉及版权等问题,请您告知,我们将及时处理!
原文始发于微信公众号(动力电池BMS):【电池PACK技术】复合材料电池箱的轻量化设计研究